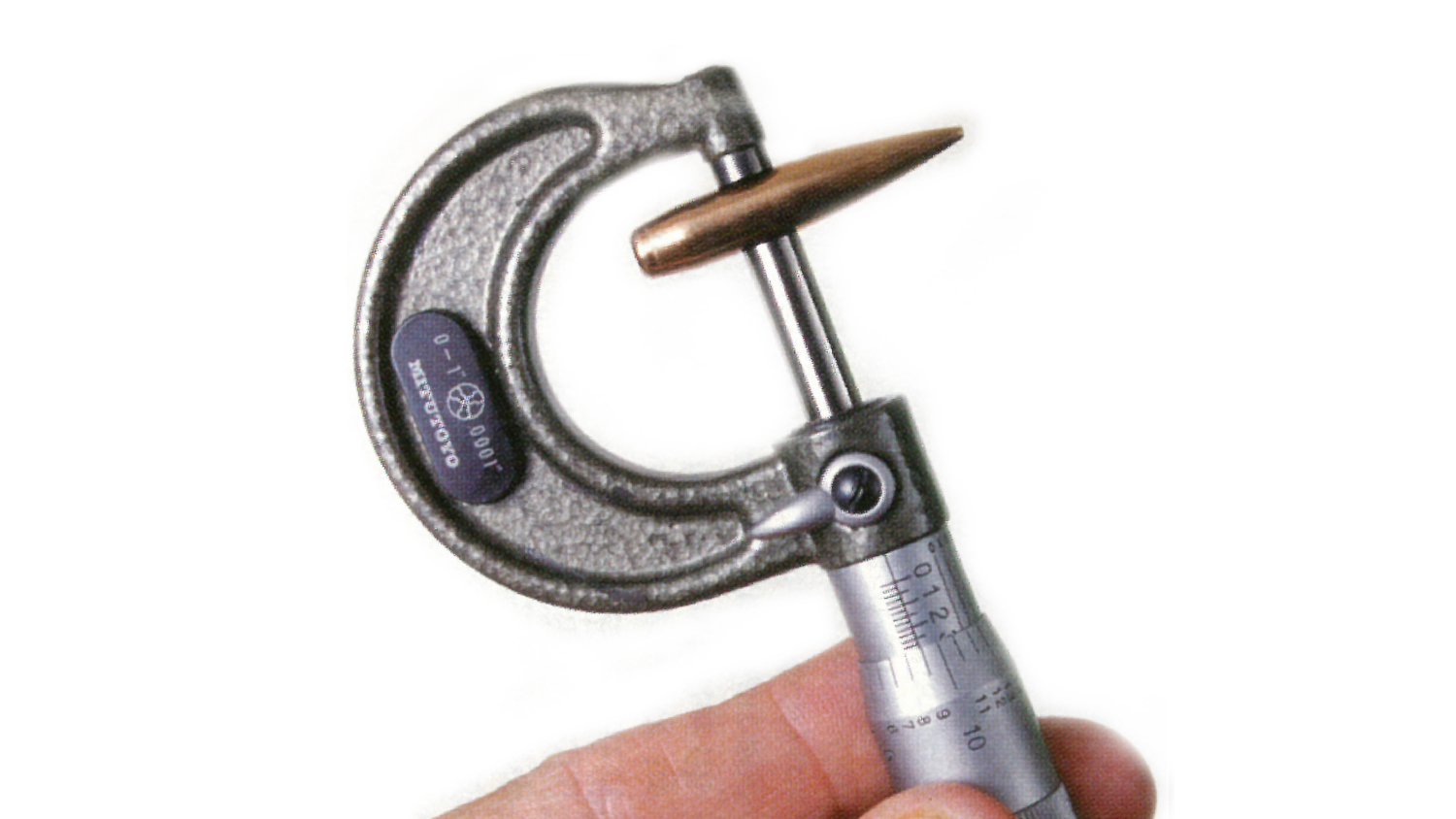
WARNING: All technical data in this publication, especially for handloading, reflect the limited experience of individuals using specific tools, products, equipment and components under specific conditions and circumstances not necessarily reported in the article and over which the National Rifle Association (NRA) has no control. The data has not otherwise been tested or verified by the NRA. The NRA, its agents, officers and employees accept no responsibility for the results obtained by persons using such data and disclaim all liability for any consequential injuries or damages.
Above: Bullets used for demanding accuracy applications should vary no more than .0001- to .0002-inch.
For many reloaders, it's enough to simply produce ammunition that is safe, economical and reasonably accurate, using standard reloading practices. Target shooters seeking optimum accuracy, however, usually employ special special reloading techniques, all of which have the same ultimate goal: to produce the maximum possible uniformity between every finished cartridge.
With uniform cartridges, all the bullets exit the muzzle at the same point in the barrel vibration pattern, giving more consistent grouping. Uniform loads also produce low shot-to-shot variation in bullet velocity, an important factor in producing consistent downrange trajectories. For example, with a typical .30-caliber target bullet, a change in the muzzle velocity from 2700 to 2770 fps produces a four-inch change in drop at 500 yards, and a 23-inch change in drop at 1000 yards—enough to pull a shot out of the 10-ring. For this reason, long-range shooters usually attempt to achieve a standard velocity deviation of no more than 10 fps.
Uniform ammunition requires cartridge components that are themselves uniform. This article presents a brief overview of many of the general techniques used by accuracy buffs—particularly benchrest competitors who are at the cutting edge of precision shooting—to select and prepare such components.
Cases
The goal of case preparation is to create a group of cases whose volume, length, neck and wall thickness, primer pockets, flash holes and so forth are all as uniform as possible.
You will not reap all the benefits of match-grade case prep, however, if your gun's chamber or breechface are misaligned with the axis of the bore. Moreover, cases fired in such a gun will fire-form to the misaligned dimensions, making them useless for extreme accuracy work.
Recognize that different brands of cases in a given caliber can vary in dimensional consistency, strength, and many other factors. For example, cases from the .308 Winchester from different manufacturers will vary by as much as 30 grains; this weight variance reflects a difference in case volume. Thus, if velocity is an issue, a brand of case having a lighter average weight will have greater internal volume, allowing you to load more powder at a safe pressure level and achieve higher velocity.
Don't forget, too, that military cases for commercial rounds—the 7.62mm NATO/.308 Win. and the 5.56mm NATO/.223 Rem.—have thicker walls and thus less case capacity than their commercial counterparts. you can make direct comparisons of case capacity by weighing cases before and after filling them with water; the difference in weight is the case capacity in grains of water.
Once you've selected the brand of case you want to use, the first step in case preparation is to sort all the cases for a particular caliber by manufacturer, date of manufacture or lot number and the number of times they have been reloaded. If you neck-size and have two or more rifles in the same caliber, segregate the cases for each gun. Rifle chambers can vary significantly, even among samples of the same make and model, and cases fired in them will vary.
For accuracy reloads, never use brass you picked up at the range, so-called "once-fired" brass sold at a store or even brass given to you by a friend; you never know what you're getting. The best are new, "virgin" cases from the same lot produced by a manufacturer, or once-fired cases produced by firing in your gun new factory ammunition from the same lot and manufacturer.
Once you've sorted your cases, inspect each case for defects such as off-center flash holes or dents in the neck or shoulder. Some benchrest shooters measure the neck thickness of each case at different spots, and discard cases having more than a .001- or .002-inch variance on the theory that a variance in neck-wall thickness also extends down into the case body. This, in turn, gives an off-center combustion chamber and an internally lopsided case that won't respond in a uniform manner to the stresses of firing.
Next, trim all cases to length, chamfer the case mouths, and then uniform the primer pockets and flash holes. These last two steps make primer and powder ignition more consistent. Numerous hand tools are available to slightly deepen the primer pockets to a uniform depth, and to remove inconsistencies in the flash-hole diameter as well as any burrs around the flash-hole inside the case. Such burrs can interfere with the flow of the primer spark, producing inconsistent powder ignition.
An important accuracy-promoting step in case prep is neck turning. This process produces a uniform neck-wall thickness, which in turn more accurately centers the bullet in the barrel throat and gives more consistent bullet pull. Neck turning is normally needed because factory brass normally has .001- to .003-inch total variation in neck-wall thickness, and sometimes as much as .006- to .007-inch.
Neck turning is also an absolute requirement for so-called "tight neck" chambers, which do not allow a cartridge with normal neck-wall thickness to be chambered. Tight-neck chambers—common on benchrest and other extreme accuracy guns—help center the bullet in the bore, and also prevent excessive working of the case neck, thus promoting longer case life. Often the clearance between the outside of the turned neck and the wall of a tight-neck chamber is only about .0005-inch per side, for a total clearance of .001-inch.
Neck-turning tools consist of a pilot of the proper diameter that fits snugly inside the neck and an adjustable cutter that shaves the outside of the neck so that neck-wall thickness is uniform all the way around. Used properly, these tools can produce neck walls that are consistent to .0001- to .0002-inch. Neck-turning is an art in itself; for example, care must be taken not to cut into the neck-shoulder junction.
Some accuracy reloaders also inside-ream their case necks, particularly when forming wildcat cases, or when neck-turning and a subsequent neck sizing produces a ring of brass (known as a "donut") inside the neck. Others ignore the donut if it does not interfere with bullet seating. Interestingly, some benchresters who have experimented with neck reaming report a slight loss of accuracy following the procedure.
Case heads that do not evenly contact the breechface of the bolt can enlarge groups. Tests by Vihtavouri show that a head that is only .002- to .003-inch out-of-true can as much as double the vertical spread. Cases with out-of-true heads are often responsible for otherwise unexplained flyers. A lathe or a Wilson case trimmer can be used to true the case heads.
Not all target shooters true their case heads; the heads will eventually fire-form to align with a trued breechface (although it may take several firings). Out-of-true case heads can be detected using a case-gauging tool. Note that if you find that the heads of all your once-fired cases are misaligned, you may have an out-of-true breechface. The best solution for this is to have a gunsmith true the breechface and reset the headspace. As a stopgap, you can mark each case (as with a small nick in the rim) and always orient the cases the same way each time they are inserted into the chamber. This ensures that the misalignment of the case head matches the misalignment of the breechface.
An additional sorting operation is required for maximum uniformity. I personally sort once-fired cases of the same lot by weight on a reloading scale, after I have trimmed them, turned their necks, and uniformed their primer pockets and flash holes. With all these steps completed before weighing, any variance in case weight reflects a difference in case volume.
Many benchresters sort their cases into classes in which the case weights vary by no more than one grain (and often much less); all the cases in one weight class have about the same capacity and are fired together. However, some successful match shooters in disciplines other than benchrest don't weigh cases at all, but rely upon shooting tests to separate the good and the bad. Cases that group well together are retained; cases producing flyers are set aside. A combination of sorting by weight and then a further culling using group shooting would seem to work as well.
Bullets
Don't bother sorting bullets by weight; today's match bullets are extremely uniform and, in any event, bullets can vary as much as 1 percent in weight without showing much of an effect on accuracy, particularly at shorter ranges. You can also sort your bullets by diameter. For match purposes, I'd select bullets whose diameters didn't vary more than .0001- to .0002-inch, and set aside those outside that limit.
The rule of thumb is that your bullets should measure about .0005- to .001-inch larger than bore (groove) diameter, although some shooters have gotten excellent accuracy with bullets as much as .0015-inch oversize in some barrels. Slugging your bore or making a Cerrosafe cast of it will allow you to measure groove diameter with precision. Internal flaws in the core, and inconsistencies in jacket thickness or cocentricity, can have a disastrous effect on grouping. For best accuracy, jacket thickness should vary no more than about .0002- to .0003-inch. Shooters seeking this level of consistency traditionally have chosen custom-made bullets made with ultra-uniform J-4 jackets, which in some lots vary as little as .0001-inch.
Also important is the true roundness of the bullet. Several manufacturers produce devices that use a dial indicator to measure bullet out-of-roundness as it is spun on an anvil. Custom target bullets typically have only about .0001- to .0002-inch runout, while commercial match bullets may have .0003-inch runout or more; cull those exceeding these standards and use them only for practice or fouling shots.
Of course, use only bullets of the same lot number to ensure that ogive profiles, jacket thickness, hardness and other parameters are as uniform as possible. Even within a single lot, manufacturing tolerances can produce slightly different ogive profiles, resulting in minute but measurable differences in seating depth. An ogive comparator can help sort bullets by their ogive profiles.
Powders
Selecting the proper powder for your accuracy load is largely a trial-and-error process, guided by information in reloading manuals as well as the experience of those who have previously worked up loads for the same cartridge. In general, powders having high loading densities (that is, most nearly fill the case) with moderate loads have the greatest accuracy potential.
The majority of target shooters, even the exacting benchrest crowd, use a powder measure to meter charges rather than weighing each charge on a scale. Most measures are able to throw charges that vary by 0.5 percent or less—enough precision for just about any purpose. Such consistency is not always possible with coarse-grained extruded powders, however, which can "bridge" or jam in the measure, preventing a full charge from being thrown. The bridged partial charge can drop with the next full charge thrown, resulting in an overcharged case.
When using a measure with extruded powders, you should throw and then weigh at least 10 consecutive charges to ensure consistency. Any more than 0.5 percent variation (about .1 grain in a .223 Rem., or .2 to .3 grain in a .308 Win.) between the heaviest and lightest thrown charges may not give top accuracy; put aside the measure and weigh all the charges. Keep in mind, too, that with maximum loads, a variation of only a few tenths of a grain can be enough to boost pressures into the danger zone.
Alternatives to slow, large-grain powders are either spherical-grained ball powders or slow-burning extruded powders having short-length grains, which usually meter through a powder measure with acceptable consistency. Of course, once you have established your load, you should continue to use powder from the same lot number to ensure maximum ballistic uniformity.
Primers
Primers from the major manufacturers are all fairly uniform and are capable of producing good accuracy. However, special "benchrest" primers have more uniform pellets of primer compound, and thus give more consistent ignition and, usually, greater accuracy.
Primer/powder compatibility is a big factor in producing accuracy, so it's worth some effort to try different combinations. Don't forget that primers vary in the spark they produce, so always reduce your powder charge slightly whenever you change primers, especially if you're putting together maximum or near-maximum loads. Magnum primers—used primarily to ignite heavy loads of slow-burning powders—may also be required to ignite some ball powders, and, in some cases, may be recommended when you are shooting below 20 degrees Fahrenheit. Only use magnum primers when the published data call for them. Also, don't substitute standard primers for magnum primers; under-ignition and inconsistent velocities can result.
Different primers have cups of different hardness, Federal primers being the softest and CCI generally regarded as the hardest, with Winchester and Remington primers falling somewhere in between. I personally wouldn't worry too much about primer cup hardness unless the firing pin of my gun produced only a marginal indentation; and in that circumstance, I'd take my gun to a gunsmith.
Some benchresters measure their primers and sort them by height, so that they can then be mechanically seated to a uniform measurable depth and a theoretically uniform seating crush, which means compression of the primer to press the anvil tight against the priming compound. Most people, however, simply seat their primers to a uniform crush by feel using a hand priming tool.
A final thought: The techniques described in this article are not all essential for every shooting discipline. Articles, books, videos and even advice from other competitors are all resources that can help you select the reloading techniques you need for your shooting activity.
Above: Bullets used for demanding accuracy applications should vary no more than .0001- to .0002-inch.
For many reloaders, it's enough to simply produce ammunition that is safe, economical and reasonably accurate, using standard reloading practices. Target shooters seeking optimum accuracy, however, usually employ special special reloading techniques, all of which have the same ultimate goal: to produce the maximum possible uniformity between every finished cartridge.
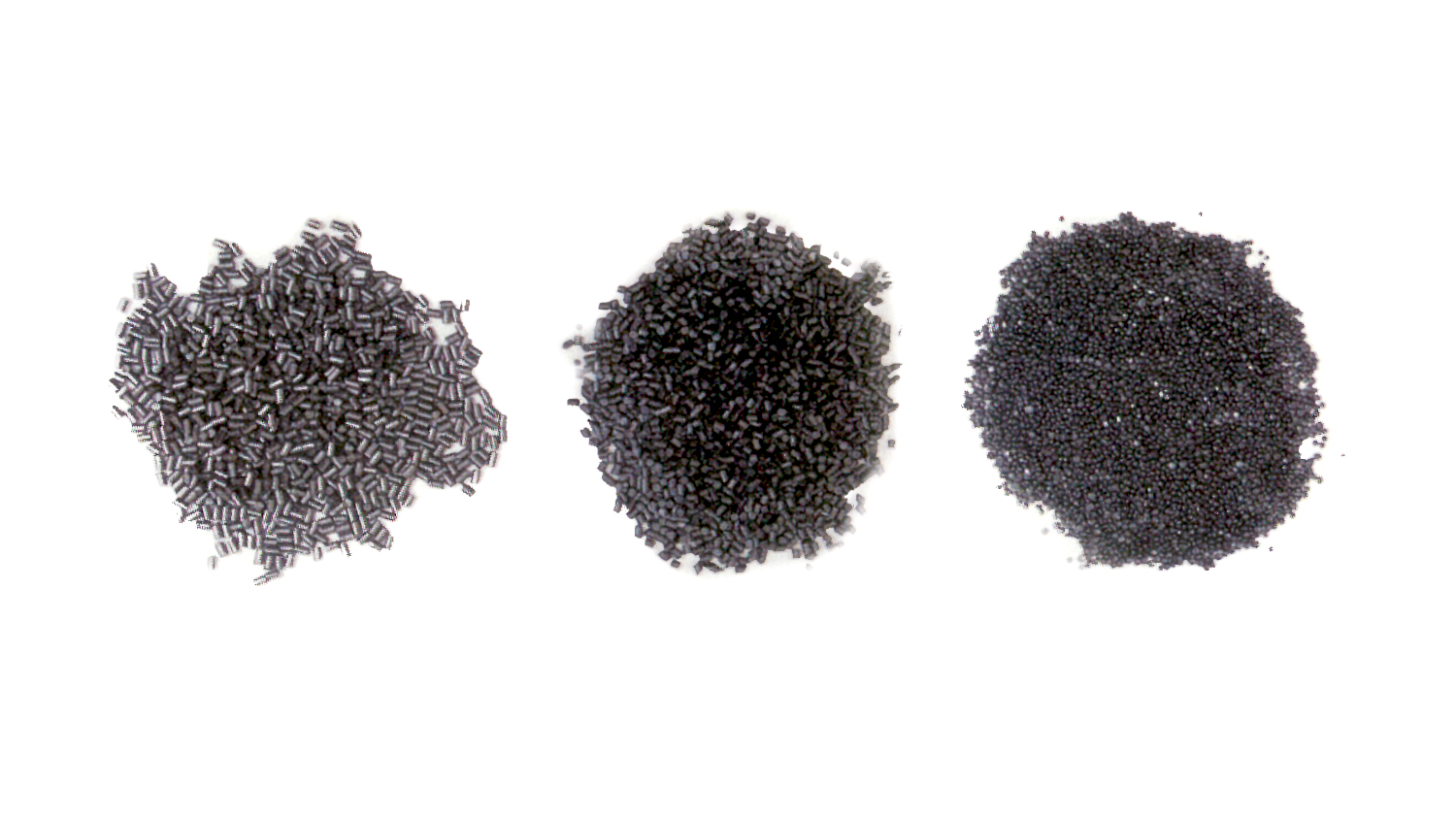
Slow-burning, long-grain extruded powders (left) may not flow smoothly and uniformly through a powder measure, and sometimes can be replaced by better-flowing ball powders (center) or short-grain extruded powders (right) having the same approximate burn rate.
Uniform ammunition requires cartridge components that are themselves uniform. This article presents a brief overview of many of the general techniques used by accuracy buffs—particularly benchrest competitors who are at the cutting edge of precision shooting—to select and prepare such components.
Cases
The goal of case preparation is to create a group of cases whose volume, length, neck and wall thickness, primer pockets, flash holes and so forth are all as uniform as possible.
You will not reap all the benefits of match-grade case prep, however, if your gun's chamber or breechface are misaligned with the axis of the bore. Moreover, cases fired in such a gun will fire-form to the misaligned dimensions, making them useless for extreme accuracy work.
Recognize that different brands of cases in a given caliber can vary in dimensional consistency, strength, and many other factors. For example, cases from the .308 Winchester from different manufacturers will vary by as much as 30 grains; this weight variance reflects a difference in case volume. Thus, if velocity is an issue, a brand of case having a lighter average weight will have greater internal volume, allowing you to load more powder at a safe pressure level and achieve higher velocity.
Don't forget, too, that military cases for commercial rounds—the 7.62mm NATO/.308 Win. and the 5.56mm NATO/.223 Rem.—have thicker walls and thus less case capacity than their commercial counterparts. you can make direct comparisons of case capacity by weighing cases before and after filling them with water; the difference in weight is the case capacity in grains of water.
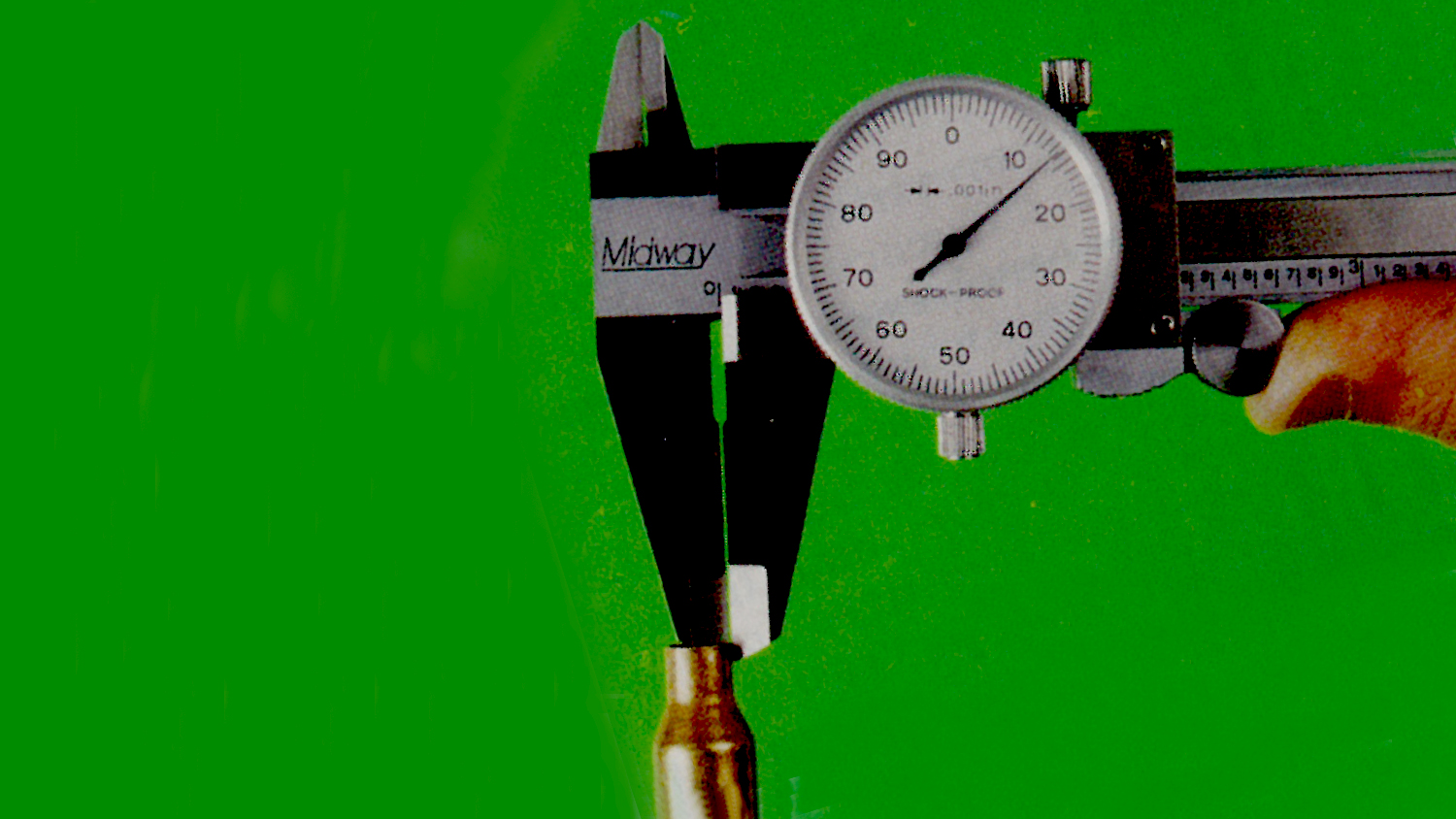
A case whose neck varies more than .002-inch in thickness in different spots should be discarded, as that variance usually also continues into the body.
For accuracy reloads, never use brass you picked up at the range, so-called "once-fired" brass sold at a store or even brass given to you by a friend; you never know what you're getting. The best are new, "virgin" cases from the same lot produced by a manufacturer, or once-fired cases produced by firing in your gun new factory ammunition from the same lot and manufacturer.
Once you've sorted your cases, inspect each case for defects such as off-center flash holes or dents in the neck or shoulder. Some benchrest shooters measure the neck thickness of each case at different spots, and discard cases having more than a .001- or .002-inch variance on the theory that a variance in neck-wall thickness also extends down into the case body. This, in turn, gives an off-center combustion chamber and an internally lopsided case that won't respond in a uniform manner to the stresses of firing.
Next, trim all cases to length, chamfer the case mouths, and then uniform the primer pockets and flash holes. These last two steps make primer and powder ignition more consistent. Numerous hand tools are available to slightly deepen the primer pockets to a uniform depth, and to remove inconsistencies in the flash-hole diameter as well as any burrs around the flash-hole inside the case. Such burrs can interfere with the flow of the primer spark, producing inconsistent powder ignition.
An important accuracy-promoting step in case prep is neck turning. This process produces a uniform neck-wall thickness, which in turn more accurately centers the bullet in the barrel throat and gives more consistent bullet pull. Neck turning is normally needed because factory brass normally has .001- to .003-inch total variation in neck-wall thickness, and sometimes as much as .006- to .007-inch.
Neck turning is also an absolute requirement for so-called "tight neck" chambers, which do not allow a cartridge with normal neck-wall thickness to be chambered. Tight-neck chambers—common on benchrest and other extreme accuracy guns—help center the bullet in the bore, and also prevent excessive working of the case neck, thus promoting longer case life. Often the clearance between the outside of the turned neck and the wall of a tight-neck chamber is only about .0005-inch per side, for a total clearance of .001-inch.
Neck-turning tools consist of a pilot of the proper diameter that fits snugly inside the neck and an adjustable cutter that shaves the outside of the neck so that neck-wall thickness is uniform all the way around. Used properly, these tools can produce neck walls that are consistent to .0001- to .0002-inch. Neck-turning is an art in itself; for example, care must be taken not to cut into the neck-shoulder junction.
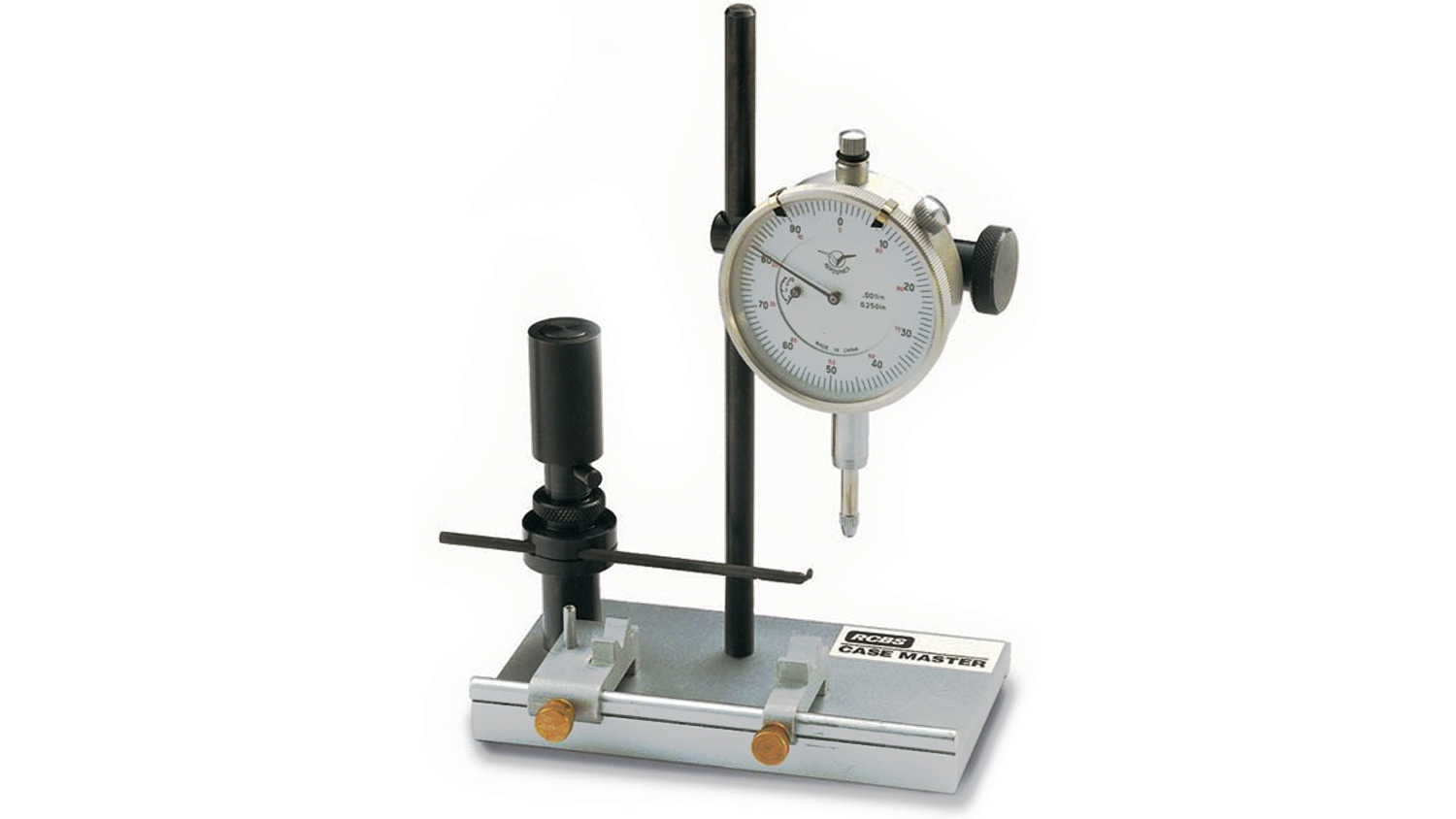
This RCBS Case Master Concentricity Gauging tool measures neck concentricity, uniformity, thickness and bullet run-out, and additionally will detect case head separation before any symptoms are apparent on the outside of the case.
Case heads that do not evenly contact the breechface of the bolt can enlarge groups. Tests by Vihtavouri show that a head that is only .002- to .003-inch out-of-true can as much as double the vertical spread. Cases with out-of-true heads are often responsible for otherwise unexplained flyers. A lathe or a Wilson case trimmer can be used to true the case heads.
Not all target shooters true their case heads; the heads will eventually fire-form to align with a trued breechface (although it may take several firings). Out-of-true case heads can be detected using a case-gauging tool. Note that if you find that the heads of all your once-fired cases are misaligned, you may have an out-of-true breechface. The best solution for this is to have a gunsmith true the breechface and reset the headspace. As a stopgap, you can mark each case (as with a small nick in the rim) and always orient the cases the same way each time they are inserted into the chamber. This ensures that the misalignment of the case head matches the misalignment of the breechface.
An additional sorting operation is required for maximum uniformity. I personally sort once-fired cases of the same lot by weight on a reloading scale, after I have trimmed them, turned their necks, and uniformed their primer pockets and flash holes. With all these steps completed before weighing, any variance in case weight reflects a difference in case volume.
Many benchresters sort their cases into classes in which the case weights vary by no more than one grain (and often much less); all the cases in one weight class have about the same capacity and are fired together. However, some successful match shooters in disciplines other than benchrest don't weigh cases at all, but rely upon shooting tests to separate the good and the bad. Cases that group well together are retained; cases producing flyers are set aside. A combination of sorting by weight and then a further culling using group shooting would seem to work as well.
Bullets
Don't bother sorting bullets by weight; today's match bullets are extremely uniform and, in any event, bullets can vary as much as 1 percent in weight without showing much of an effect on accuracy, particularly at shorter ranges. You can also sort your bullets by diameter. For match purposes, I'd select bullets whose diameters didn't vary more than .0001- to .0002-inch, and set aside those outside that limit.
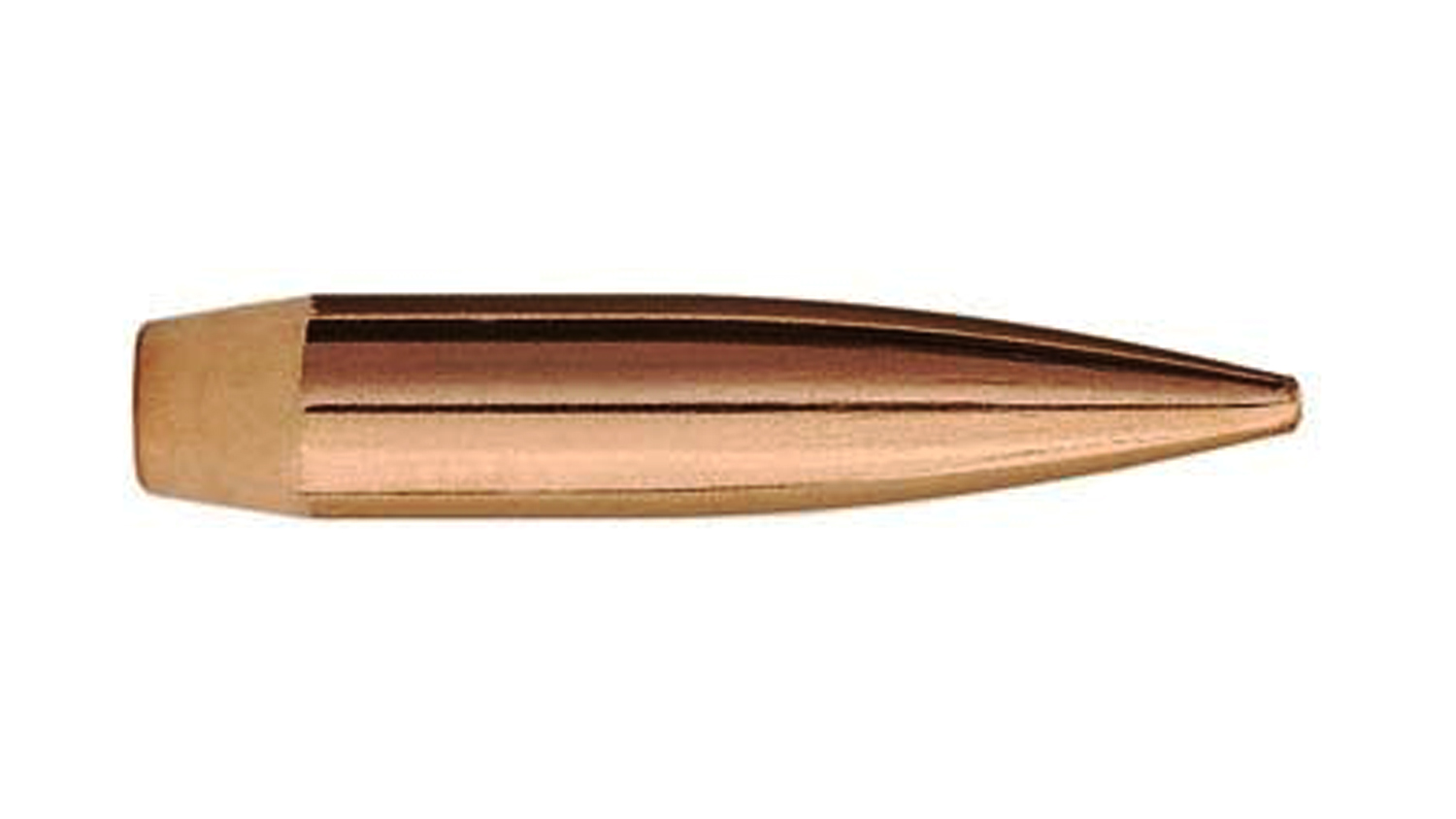
Modern match bullets, such as this Sierra 6mm 107-grain MatchKing HPBT, are extremely uniform.
Also important is the true roundness of the bullet. Several manufacturers produce devices that use a dial indicator to measure bullet out-of-roundness as it is spun on an anvil. Custom target bullets typically have only about .0001- to .0002-inch runout, while commercial match bullets may have .0003-inch runout or more; cull those exceeding these standards and use them only for practice or fouling shots.
Of course, use only bullets of the same lot number to ensure that ogive profiles, jacket thickness, hardness and other parameters are as uniform as possible. Even within a single lot, manufacturing tolerances can produce slightly different ogive profiles, resulting in minute but measurable differences in seating depth. An ogive comparator can help sort bullets by their ogive profiles.
Powders
Selecting the proper powder for your accuracy load is largely a trial-and-error process, guided by information in reloading manuals as well as the experience of those who have previously worked up loads for the same cartridge. In general, powders having high loading densities (that is, most nearly fill the case) with moderate loads have the greatest accuracy potential.
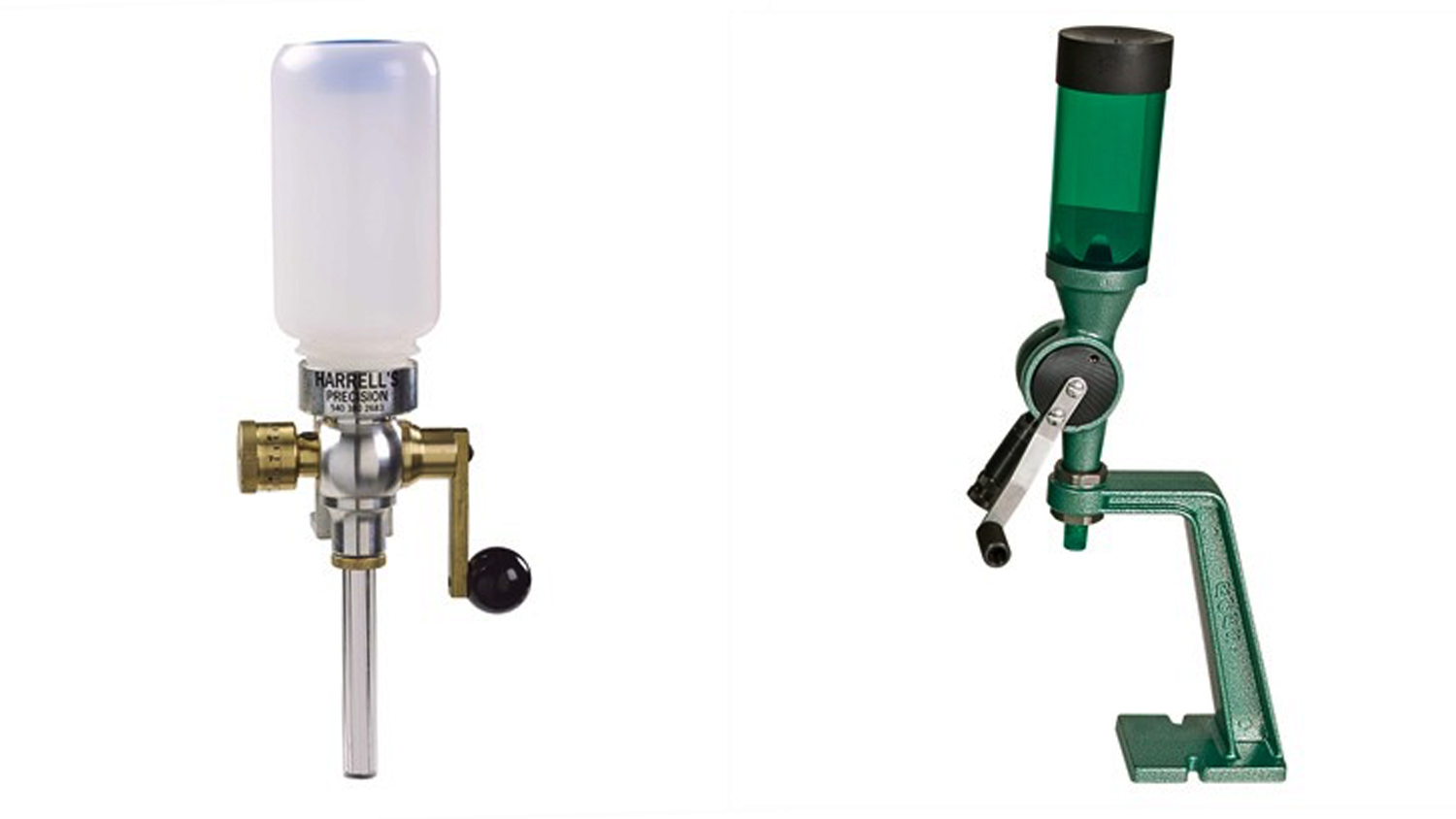
The Harrell Schuentzen measure (left) is a highly-accurate small charge measure—each click of the Culver metering system changes charge weight by approx. .03 grains. The precision ground metering drum in this RCBS Competition Powder Measure (right) will accurately meter, by volume, all types of smokeless powder—ball, flake or cylindrical (stick) with accuracy to 0.5 grains.
When using a measure with extruded powders, you should throw and then weigh at least 10 consecutive charges to ensure consistency. Any more than 0.5 percent variation (about .1 grain in a .223 Rem., or .2 to .3 grain in a .308 Win.) between the heaviest and lightest thrown charges may not give top accuracy; put aside the measure and weigh all the charges. Keep in mind, too, that with maximum loads, a variation of only a few tenths of a grain can be enough to boost pressures into the danger zone.
Alternatives to slow, large-grain powders are either spherical-grained ball powders or slow-burning extruded powders having short-length grains, which usually meter through a powder measure with acceptable consistency. Of course, once you have established your load, you should continue to use powder from the same lot number to ensure maximum ballistic uniformity.
Primers
Primers from the major manufacturers are all fairly uniform and are capable of producing good accuracy. However, special "benchrest" primers have more uniform pellets of primer compound, and thus give more consistent ignition and, usually, greater accuracy.
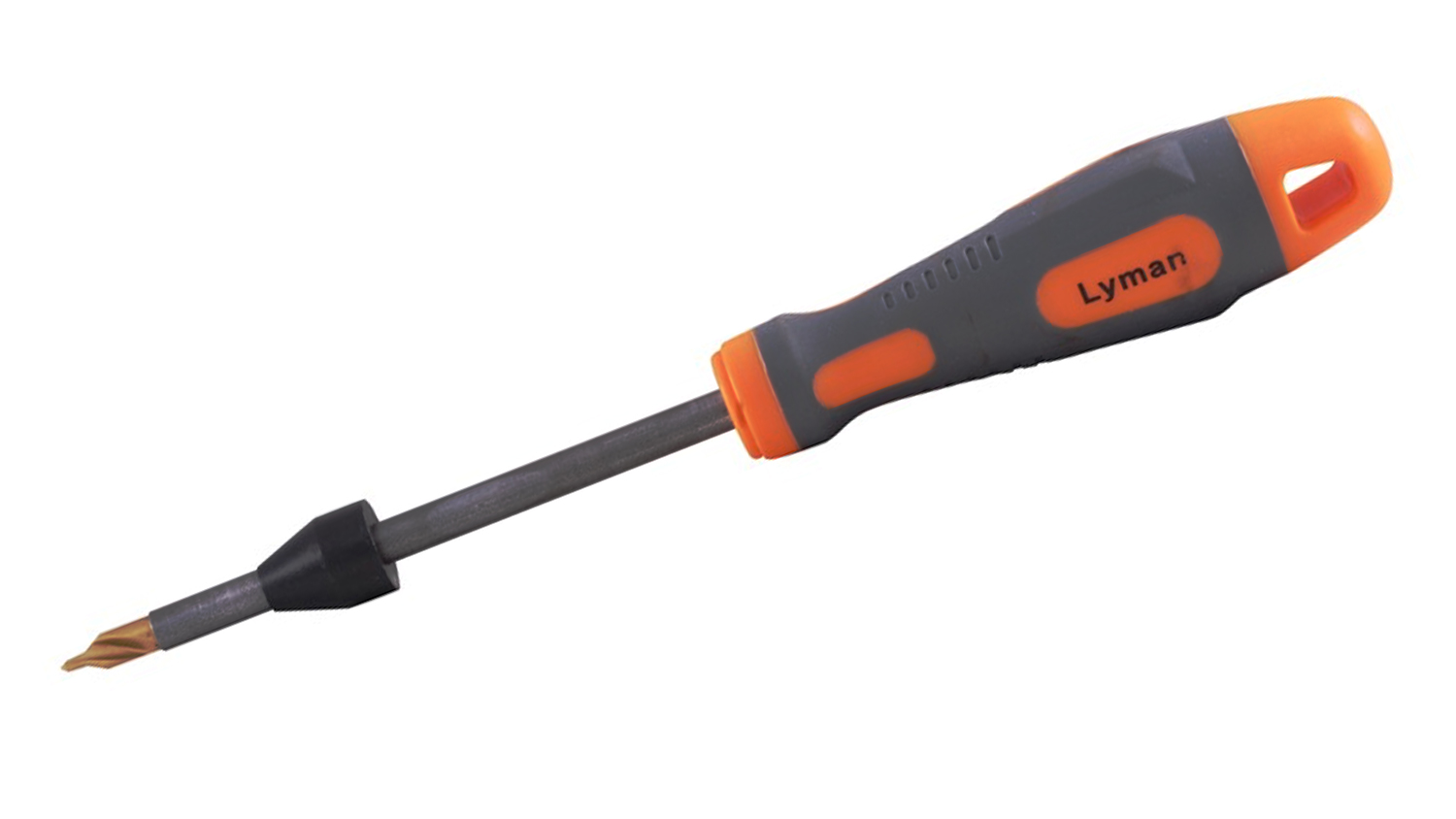
This Lyman flash-hole uniforming tool has a tip that uniforms the flash-hole diameter; the angled part of the cutter removes burrs from the mouth of the flash hole inside the case.
Different primers have cups of different hardness, Federal primers being the softest and CCI generally regarded as the hardest, with Winchester and Remington primers falling somewhere in between. I personally wouldn't worry too much about primer cup hardness unless the firing pin of my gun produced only a marginal indentation; and in that circumstance, I'd take my gun to a gunsmith.
Some benchresters measure their primers and sort them by height, so that they can then be mechanically seated to a uniform measurable depth and a theoretically uniform seating crush, which means compression of the primer to press the anvil tight against the priming compound. Most people, however, simply seat their primers to a uniform crush by feel using a hand priming tool.
A final thought: The techniques described in this article are not all essential for every shooting discipline. Articles, books, videos and even advice from other competitors are all resources that can help you select the reloading techniques you need for your shooting activity.