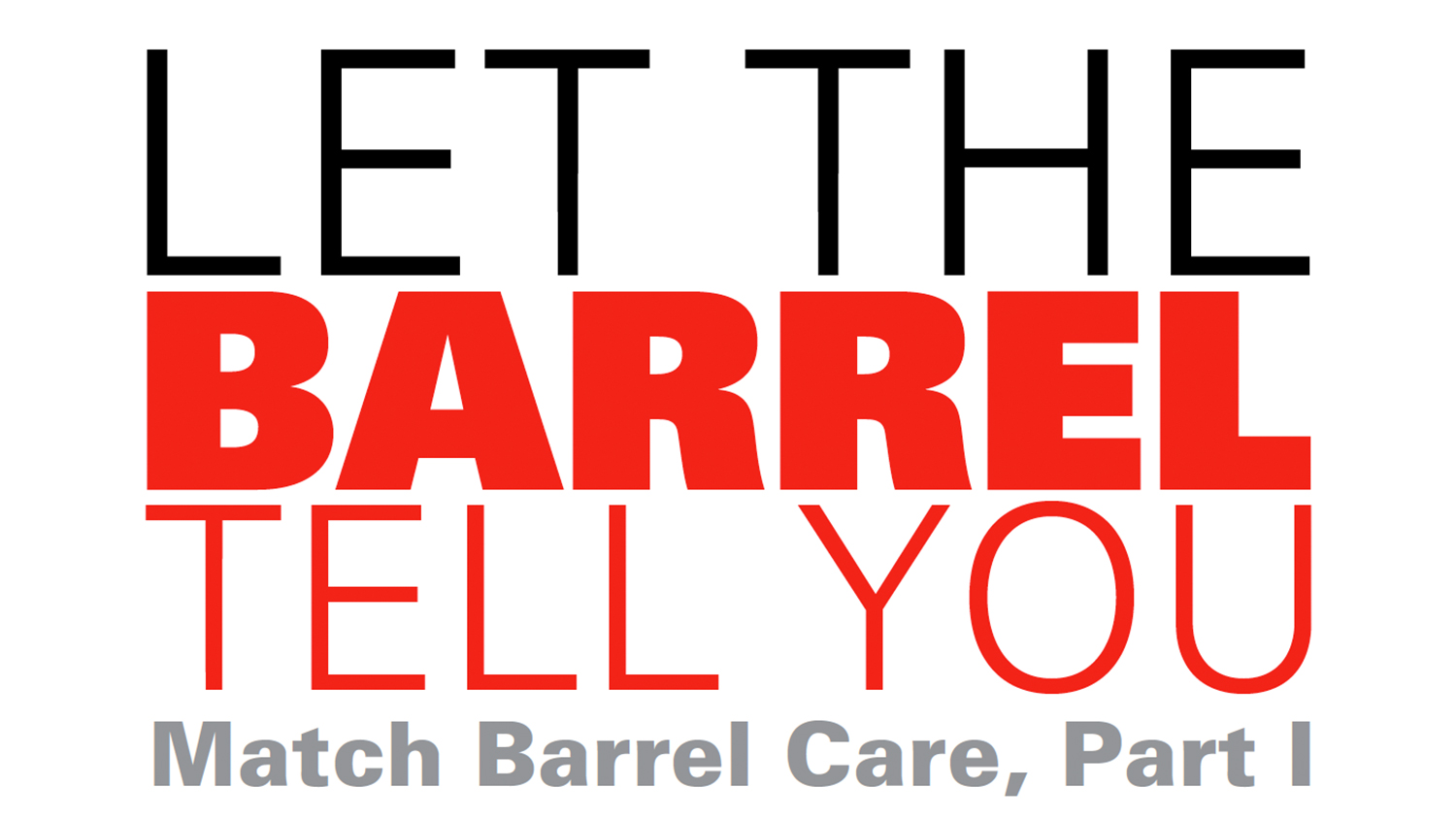
Why worry about a little barrel fouling when the throat is subjected to a brutal 5600° F volcano at 55,000 PSI? To investigate these and other questions about taking care of a match barrel, we spoke with a dozen experts and share their knowledge in this article.
After listening to folks who shoot, build barrels or manufacture cleaning solvents for a living, we concluded that even the experts each have their own unique recommendations on how to care for a match barrel. But they all agree on one thing—the gun will tell you what it likes best. Because the life expectancy of a match barrel is about 1500 to 2500 rounds, the objectives of cleaning one should include: preserve accuracy, slow the erosion and remove fouling—all without damaging the gun. This article doesn’t claim that one cleaning method is better than the next. Rather, we set out to interject a little science into the discussion and to share some lessons learned from experts in the field.
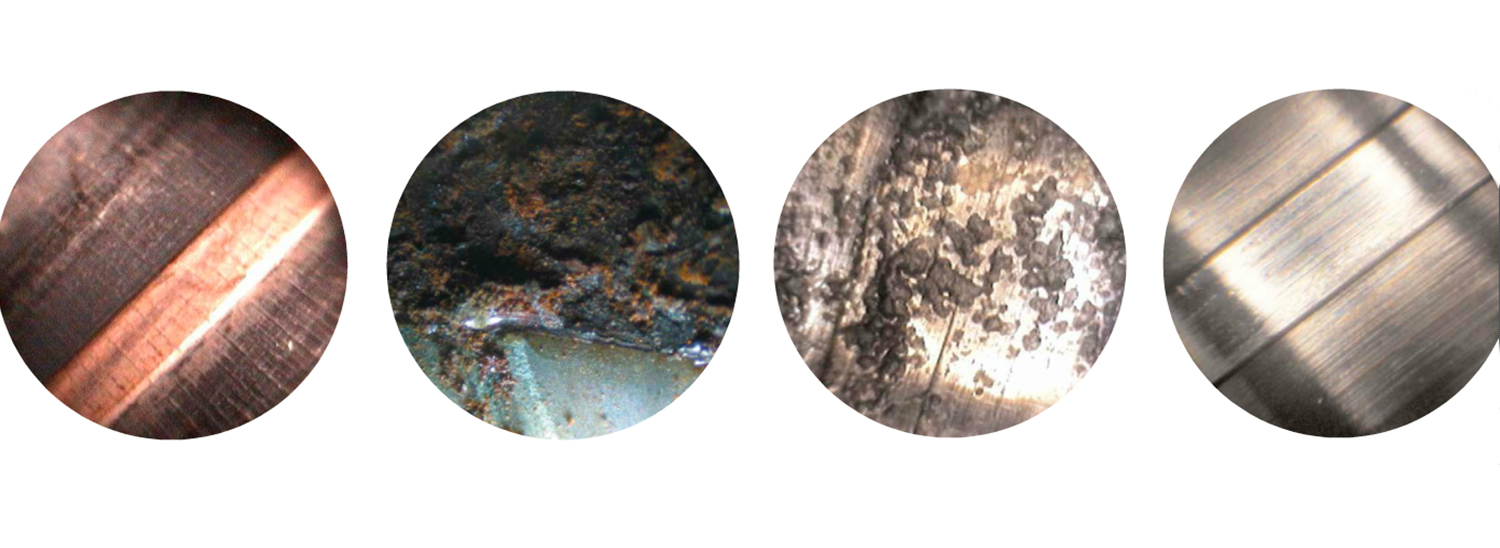
Chemistry 101
Several conversations with our experts began with: “Well, I’m not a chemist, but …” So, to better understand the chemical aspects of gun cleaning, we spoke with three experienced people in that industry.
William B. Smith is the owner of FTI, Inc., a manufacturer of specialty lubricants and solvents that is best known in the firearms industry as the manufacturer of the Tetra Gun care product line. FTI also supplies gun cleaners and lubricant products to other gun care companies under private label arrangements.
Frank Ventimiglia, co-owner of Shooters Choice Co., has been in business since his father Sal started the company as a benchrest shooter in search of a better cleaner. The company began as Marksman’s Choice in May 1983 and changed four years later to the name we know today.
Chris Fazio is the General Manager and COO of KG Industries. KG was founded to provide dry film lubricants and thin film protective coatings to the aerospace, military, sporting goods and motor sports industries. In 1998 they began producing the original Gun Kote formulas, an extensive line of gun care products and a line of Micro PTFE Lubricants. KG also distributes gun cleaners and lubricant products under private label arrangements.
What follows, and is continued in Part 2, are notes from the discussions about chemistry with these three gentleman. Cleaning products that are designed to oxidize or emulsify fouling for easier removal have similar goals. Some, however, introduce chlorine or ammonia salt that must be diluted or neutralized after their use. Some products are more aggressive at removing fouling to reduce cleaning time, a topic we discuss at length in Part 2. Critical to product selection for competitive shooters is learning which cleaning recipes actually retard the fouling process to begin with. Lubricating the barrel in a way that postpones fouling is more important to competitors than removing the fouling after the match has been lost.
Carbon Fouling
Rust: Powder residue (carbon) can act like a desiccant, just like the little packets that come with your scope. A desiccant attracts moisture—enough said.
Diamond Dust in Your Barrel: Like the formation of a diamond, heat and pressure can transform carbon fouling into a ceramic layer that is difficult to remove. Any excessive work required to remove this neglected accumulation of carbon fouling can cause damage to the bore and throat. “An ounce of prevention is worth a pound of cure,” means we should clean sooner and more often.
Firecracking: Powder that accumulates in the throat can behave like a piece of charcoal. Under extreme heat, this reignited carbon fouling will accelerate throat erosion.
Master gunsmith David Sams, formerly of the AMU, recommends putting a patch soaked with bore cleaner through the bore immediately after completing a stage of fire to avoid this ceramic layer of carbon build-up. This sounds like the advice from a dentist: “Once the plaque has built-up, it’s too late for toothpaste.”
Copper Fouling
Pitting: A wet cell battery is a galvanic cell that contains two different (dissimilar) metals and a solution between them that helps transfer ions from one metal element to the other. In a match barrel with copper fouling (two dissimilar metals), the “least noble” metal is the one being depleted, also referred to as corrosion, etching or pitting. Because the barrel’s chromium, iron or nickel are “less noble” than copper or carbon, the barrel metal will corrode in their presence. What this means for shooters is that bore cleaner, left in a heavily copper-fouled barrel, creates a wet-cell battery that may pit or etch the barrel. And if there is a high concentration of ammoniated solvent left in the barrel, the trip to the barrel graveyard will be even swifter.
Bondo: Like using Bondo putty to smooth auto dents, a little copper fouling can fill imperfections in the barrel. Shooters will often sight-in with a few “fouler shots” for this purpose. Let the barrel “tell you” what it prefers.
Barrel Break-In
When choosing a barrel alloy, the builder is looking for a relatively stiff barrel with some expansion at the throat to avoid being too brittle under pressure, soft enough for deep-hole drilling and rifling, and hard enough to survive high-velocity bullet friction. The favorite alloys of today’s barrel builders are chrome moly and stainless steel.
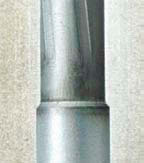
Chrome moly: Sometimes written as chromoly, chrome moly gets its name from the two main ingredients: chromium and molybdenum (pronounced “mo-lib-de-num”). This mixture (alloy) of steel has a very high tensile strength that is useful for products like aircraft tubing, race car roll cages or rifle barrels. Because chrome moly is harder than stainless steel, there is some evidence that chrome moly barrels retain their accuracy longer, but the throats may fail sooner. Because chrome moly can rust, it is typically blued to guard against oxidation. A popular recipe for chrome moly is 4130, which is a numbering system devised by the American Iron and Steel Institute (AISI). The last two numbers—‘30’ reference a carbon content of nominally 0.30 percent. Therefore, 4140 chrome moly has more carbon content than 4130 and so has a higher tensile strength.
Stainless Steel: Developed just before WWII to improve carbon steel cutlery, stainless steel (SS) is a more recently developed alloy of steel, chromium and other elements that make it less susceptible to rusting, but not rustproof. 416R SS is a popular choice among barrel makers. Because SS is softer than chrome moly, a stainless barrel is easier to hand-lap for a finer finish and provides some elasticity in the throat.
By purchasing steels directly from the steel mills, the builder can specify their preferred chemistry and heat treatments. This is partially the reason for different break-in and cleaning instructions from different barrel makers. Here are some observations collected during the interviews about chrome moly versus SS:
David Sams observed: “Each of these materials has its own merits. Both have the same accuracy potential in my experience. Stainless steel resists corrosion better than chrome moly, but is not as abrasion resistant. I’ve noticed that the barrel throat seems to last longer in the stainless barrel, but not the bore.”
Dan Lilja comments: “I’ve noticed that, given an equal interior finish in both stainless steel (416R) and chrome moly (4142), the chrome moly barrel will copper foul more.”
Pistol vs. Rifle Barrels: While these discussions are relevant to pistol shooters, the bullet velocity is slower with a shorter pistol barrel and therefore results in less fouling and erosion, depending on bullet jacket choice.
Carroll Pilant of Sierra Bullets shared: “We use the same 95-5 copper (95 percent copper and 5 percent zinc) material for both rifle and pistol bullets. It is basically the higher velocities and pressures that produce more fouling in a rifle barrel. You can still get copper fouling in a pistol barrel, but it isn’t nearly as drastic as in a rifle barrel.”
Lilja adds: “It has been my experience that longer barrels and faster twists tend to foul more. As Fred Barker points out, however, this could be caused more by long bullets than the barrel.”
The Break-in Routine: The reason for breaking-in a high-quality, handlapped barrel (versus a production barrel with imperfections such as poor bore-chamber alignment) is to ensure that it shoots to its precision potential, performs consistently and cleans easily. If the hand-lapped barrel and finely reamed throat are such that it accumulates relatively little copper fouling, then the gun may shoot consistently without much break-in. Because barrel makers often select their own recipe for barrel materials and employ their own finishing techniques, they have good reason to make specific recommendations on how best to maintain their barrels.
Tim North of Broughton Barrels and the 5C rifling trademark shares: “The total break-in of the bore to stabilize velocities is nominally achieved at 100 rounds on most brands of barrels on the market. The first 40 rounds will be relatively slow. Velocity will start increasing between 40-70 rounds. Many break-in and cleaning methods work well. We have used our present method with success. Do not break-in an unlubricated bore. High-temperature synthetic oil is best.”
Lilja continues: “It is important to remove fouling after each break-in shot to help prevent excessive buildup later on. Do not use moly-coated bullets during the break-in procedure. Clean after every shot for the first 10-12 rounds or until copper fouling stops.” On barrel making, Lilja also comments that: “We’ve experimented with different techniques and have settled on what we believe gives us the best finish. Though it may surprise some, lapping to a finer finish will result in an increase in fouling. A barrel can be too smooth.”
Shilen Rifles, Inc. writes: “Break-in procedures are as diverse as cleaning techniques. Shilen introduced a break-in procedure mostly because customers seemed to think we should have one. By and large, we don’t think breaking-in a barrel is a big deal [since all of our barrels are hand-lapped]. However, don’t just push bullets down the barrel during break-in. This is a great time to begin load development. Also, a rifle barrel does not have to be spotless to shoot great. Many times more harm than good is done trying to get it that way. [Paraphrased] Like body putty on a car dent, small amounts of fouling can fill imperfections in a barrel. Since copper usually comes out with the powder, benchrest shooters will typically shoot 1 to 2 ‘fouler shots’ before beginning their record shots in order to re-foul the barrel for improved accuracy.”
Frank Green of Bartlein Barrels states: “For the most part, the only thing you are breaking-in is the throat area of the barrel. The nicer the finish that the finish reamer or throating reamer leaves, the faster the throat will break-in. Shoot one round and clean for the first two rounds individually. Look to see what the barrel is telling you. If I’m getting no copper out of it, I shoot the gun.”
John Kreiger: “Initially you should perform the shoot-one-shot-and-clean cycle for five cycles. If fouling hasn’t reduced, fire five more cycles and so on until fouling begins to drop off. At that point shoot three shots before cleaning and observe. If fouling is reduced, fire five shots before cleaning. It is interesting to record shot groups during the three and five shot cycles.” The table below is from the Kreiger website.
Note that a particular barrel can shoot accurately and foul more than others. Whether a well-lapped barrel with a perfectly smooth throat needs to be broken-in is a question that apparently only your barrel can answer.
So, the consensus on break-in seems to be: Shoot one round and clean for the first 5 rounds individually (or as recommended by your barrel maker for warranty reasons). Look to see what the barrel is “telling” you. If you find little to no copper residue on the patch (blue or green depending on the bore cleaner used), then shoot two 5-shot groups. (Fewer than five shots leaves you open to random groupings that are not statistically representative of the gun’s true precision.) Clean the gun again and “read” the patches. If there is less friction when pushing the patch through the bore, little if any copper residue on the patches and the gun produces a small group, consider the break-in completed.
Miscellaneous quotes from our interviews:
“Just because someone does it differently, doesn’t mean it’s better or worse.”
“More damage is done by cleaning than shooting.”
“Some barrels can quit shooting without warning.”
“Once it’s a fouler, the accuracy won’t come back.”
In Part 2, we will inventory cleaning methods used by several national champions, list some lesser-known as well as household-name cleaning products and talk about how to make cleaning easier, in order to do it more often.
Our sincere thanks to the following contributors for their time and shared information:
- Gradient Lens borescope video of heat cracking, extreme wear and other bore examples, www.gradientlens.com/default.aspx
- Chris Fazio, COO KG Industries, www.kgcoatings.com
- Bill Smith, Owner FTI, Inc. (Tetra) www.tetraproducts.com/default_nf.asp *
- Frank Ventimiglia, Co-owner, Shooter’s Choice, www.shooters-choice.com *
- Master gunsmith David Sams, www.samscustomgunworksusa.com
- Custom pistol barrel maker Kevin McIntyre (KKM), www.kkmprecision.com
- Custom rifle barrel maker Boots Obermeyer, www.obermeyerbarrels.com *
- Custom rifle barrel maker Tim North (Broughton), www.rifle-barrels.net *
- Custom rifle barrel maker Frank Green, www.bartleinbarrels.com *
- Custom rifle barrel maker John Krieger, www.kriegerbarrels.com *
- Custom rifle barrel maker G.R. Douglas, www.douglasbarrels.net *
- Custom rifle barrel maker Dan Lilja, www.riflebarrels.com *
- Custom rifle barrel maker Wade Hull, www.shilen.com *
- Sierra Bullets’ Carroll Pilant, www.sierrabullets.com
- Armalite’s library of Tech Notes, www.armalite.com *
- AR-15 maintenance articles by Glen Zediker, www.zediker.com *
- Rifle Accuracy Facts by Harold R. Vaughn
* This website contains downloadable cleaning or break-in instructions.
Have a remark, complaint or suggestion? Let us know at [email protected].