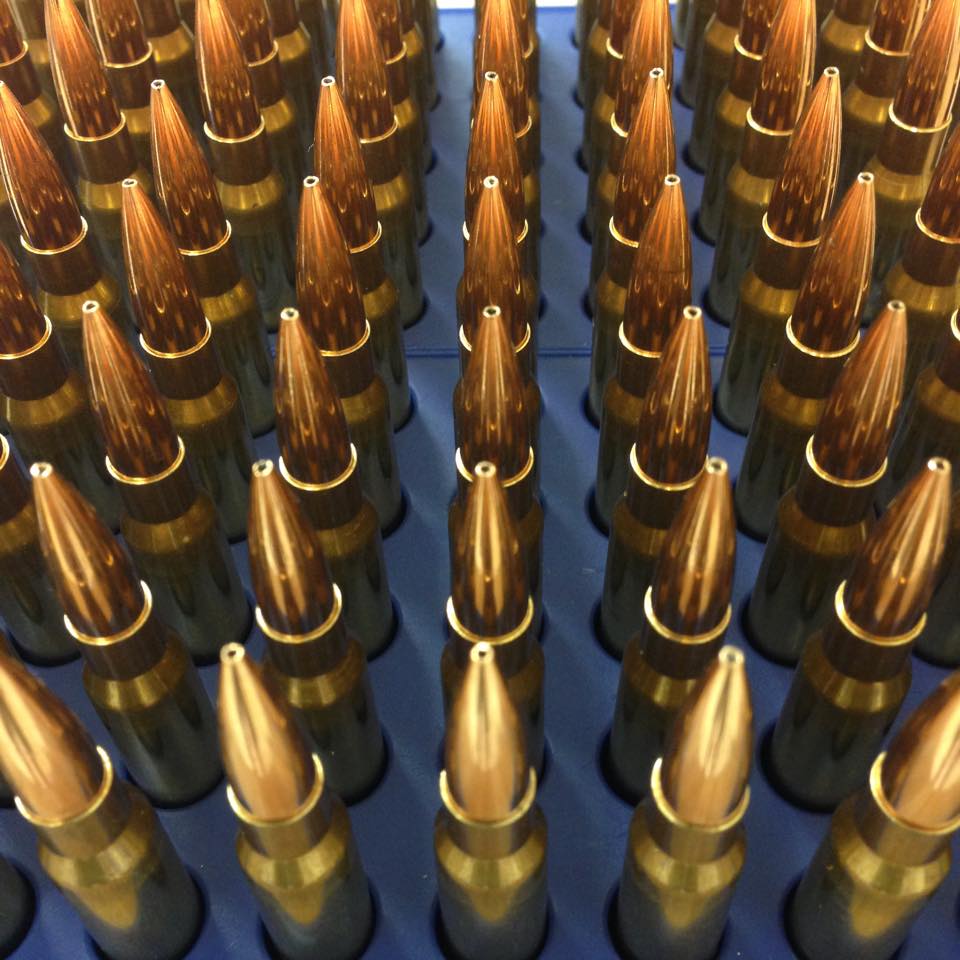
WARNING: All technical data in this publication, especially for handloading, reflect the limited experience of individuals using specific tools, products, equipment and components under specific conditions and circumstances not necessarily reported in the article and over which the National Rifle Association (NRA) has no control. The data has not otherwise been tested or verified by the NRA. The NRA, its agents, officers and employees accept no responsibility for the results obtained by persons using such data and disclaim all liability for any consequential injuries or damages.
Today, we conclude our three part series on variables that affect pressure. Readers may want to see the previous installments Part 1 and Part 2 with helpful tips on inadvertently exceeding the boundaries of known, safe data. Reminder, this guide is by no means all-inclusive!
Loading manuals frequently caution readers to re-develop loads whenever changing a major component: bullet, primer, cartridge case or even powder lot to avoid possible pressure problems. Many other variables affect pressure—one is bullet engraving force.
This is an obvious concern when using cast lead bullet data (i.e., very low engraving force) to load jacketed bullets. They have a much higher engraving force and can develop higher pressures or faster pressure spikes. However, cup-and-core bullet jackets vary greatly in thickness depending upon the design and maker, which can significantly affect pressure.
The percent of antimony in bullets’ lead cores affects hardness, and thus pressure. Bullets with similar weights but different ogive shapes can put one bullet well off the rifling at a given cartridge length, whereas another at the same length engages the rifling heavily, etc. These days, bullets are progressively being made of solid copper or other non-traditional materials. Depending upon the bullet design, this can significantly increase engraving force.
An early pioneer in solid copper bullet manufacturing instructed users to seat bullets 0.050” or greater from the rifling, which helped reduce pressure and improved accuracy. Later designs incorporate machined rings in the bearing area that reduce bore contact (BSL). They also allow the copper engaging the rifling to deform into the relief areas, reducing fouling.
The foregoing is not intended to start readers calculating which bullet designs they might launch just below light-speed while ignoring published load data. Rather, it is intended to help beginning handloaders see a few of the less-obvious variables that can affect pressure. There are many more.
Avoiding the temptation to make assumptions beyond the known data, act upon them and then place one’s face behind 60,000 PSI seems wise!
And now, we bring you another mishap story.
Decades ago, a gun store owner of the writer’s acquaintance reported the following: a friend had asked him to reload some .30-30 ammunition for his trusty Winchester 94. Despite knowing better, he grabbed a popular reloading manual, found the powder and charge giving the highest velocity for his bullet weight, and commenced assembly.
Later, his friend asked, “What did you put in those things, rocket fuel? Every time I shoot it, it blows the lever open!” The proprietor wasted no time in retrieving the thermo-nuclear cartridges and replacing them with a more sedate version. Only luck and John Browning’s design talents prevented a spectacular, instant disassembly!
Handloading is a safe, fascinating and very rewarding pastime when done correctly. Just remember, be safe out there! When researching data for new load development, always use the most recent data available, and check more than one reloading manual. Cross-checking can give valuable insights into differences between individual barrels, barrel length effects, and bullet designs.
Avoid any temptation toward wildly impetuous ballistic experiments, and enjoy the shooting sports for many happy years to come!
Thanks to the U.S. Army Marksmanship Unit for allowing the reprint of their excellent handloading series.