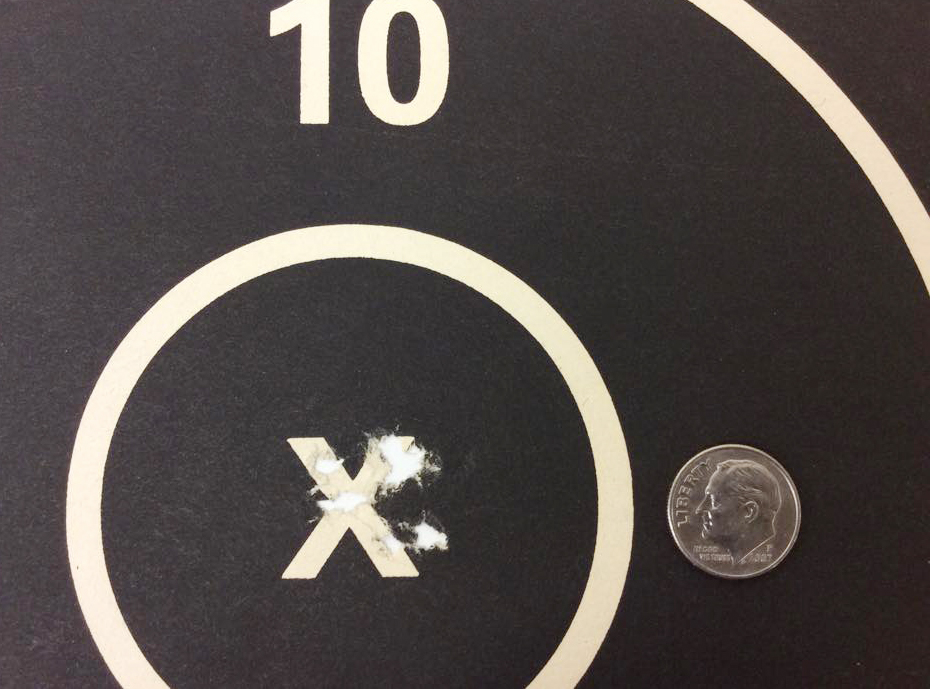
WARNING: All technical data in this publication, especially for handloading, reflect the limited experience of individuals using specific tools, products, equipment and components under specific conditions and circumstances not necessarily reported in the article and over which the National Rifle Association (NRA) has no control. The data has not otherwise been tested or verified by the NRA. The NRA, its agents, officers and employees accept no responsibility for the results obtained by persons using such data and disclaim all liability for any consequential injuries or damages.
Previously, we discussed the effects of bullet bearing surface length (BSL) and other variables that can affect pressure and velocity when developing handloads. Readers who missed Part 1 may wish to go back and review our discussion on measuring bullet bearing surface length (BSL). We discussed an approximate method of measurement, plus avoiding a possible pitfall.
But, wait, there’s more! What we measured was the pre-firing bearing surface length. Remember the long, gradual taper of the RN/FB bullet before it reached full diameter? When the bullet is thrust forward upon ignition, it is pressure-swaged to fit the bore. Given the bullets’ long, tapered portion which is just slightly under 0.284”, some portion of that becomes bearing surface.
Thus, the “official” 0.284” BSL that we measured isn’t the only bullet bearing surface engagement effect in play. This less-obvious factor will contribute to the pressure curve rate and total chamber pressure. Now, how much total bearing surface length (during firing) is there? Hmmm … The calipers didn’t show us that …
So, what is the effect of any bullet’s post-ignition BSL upon chamber pressure? It includes many variables: e.g., jacket thickness and material, core hardness, bore diameter, throat type, rifling form, bullet “jump” to rifling, propellant burn rate, etc.
Now, picture the vast array of bullet designs and constructions, powders with different burn rates, etc.
The logical answer to accurately predicting these effects on pressure without rather complex computer input and modeling is, “I don’t know.” That’s no problem. I don’t NEED to know. What I DO need is to maintain respect for the pressures and variables involved, and develop handloads carefully, knowledgeably and with due caution. The key take-away point is, “Now I KNOW what I don’t know.”
Consider (hypothetical) Bob, who loves his classic, pre-war M1903 Mannlicher-Schoenauer 6.5x54 mm sporter. He just found a major bargain on its preferred 160 grain RN/FB bullets. The local sporting goods store sold him several hundred rounds of World War II, German-manufactured 6.5x53R Dutch Mannlicher ammo loaded with these bullets. They were extremely cheap because the case necks had cracked in storage.
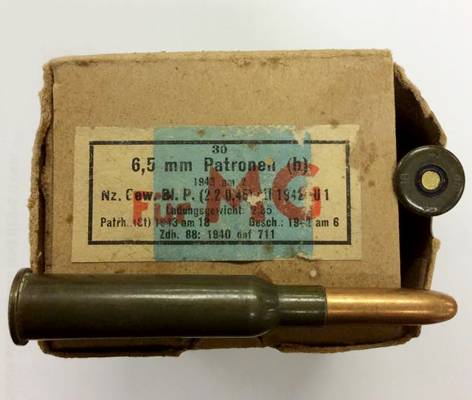
That was no problem—all he wanted was the bullets, and they were of the correct design, weight and diameter for his rifle. Heck, he could even pull them just using his fingers—they were pristine! What could possibly go wrong?
Bob wasted no time in seating his new bargain bullets over his long-time favorite, maximum hunting powder charge. He “knew” the load data was good, as he’d carefully developed it in his rifle using high-quality soft-points. He had chronographed his increasing loads while observing for pressure signs until he reached the correct velocity with a safe charge, as per his manual. All was normal, case life and accuracy were excellent.
Upon firing the new Franken-ammo, however, things changed … quickly and drastically. His beloved hand-built, highly valuable Austrian sporter blew a primer, and the stock was wrecked.
Why?
Well, war-time being what it was, the Germans conserved copper by using steel jackets for their ammunition, with an extremely thin copper “flash." Naturally, steel reacts to pressure a bit differently than the copper jackets Bob had used earlier. Had Bob thought about it, he could have checked the jacket material with a magnet …
And, being military, the steel jackets were thick. They were designed for barrier penetration, rather than expansion. Moreover, the German core material was not virgin, soft lead, but a harder alloy. Bob’s “find” was no bargain. It was a net loss on his beloved, irreplaceable rifle—but luckily, he did not lose any beloved, irreplaceable fingers or eyes. This time.
Hopefully, this dramatic, if fictional, episode will help ingrain an image into the reader’s memory. Perchance it will even leap to mind like a cautionary Jiminy Cricket, should readers be tempted to experiment a bit too exuberantly. Join us again next week for the conclusion of this handloading safety series, plus another of our thrilling, true-life “Don’t Be That Guy” episodes.
Attention to detail is our watchword for today. Shoot well!
Thanks to the U.S. Army Marksmanship Unit for allowing the reprint of their excellent handloading series.