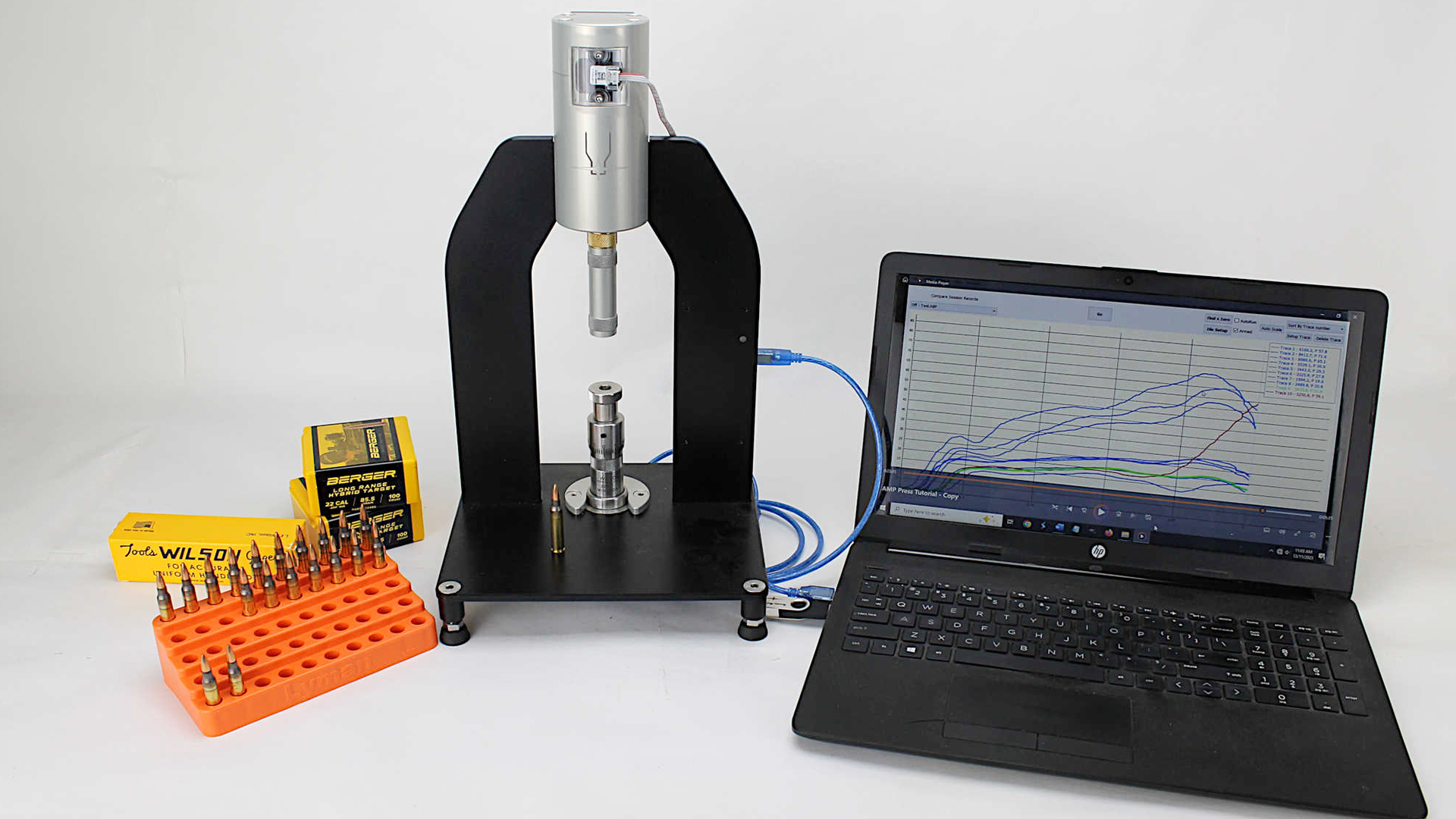
Handloading competitors working at the razor edge of precision—real precision in serious pursuit of onehole groups or a 200-20X at long range or extending the definition of “long-range precision”—have available a remarkable new tool. The AMP Press is essentially an electronic bullet seater that connects to your computer to show whether neck tension is consistent from cartridge to cartridge.
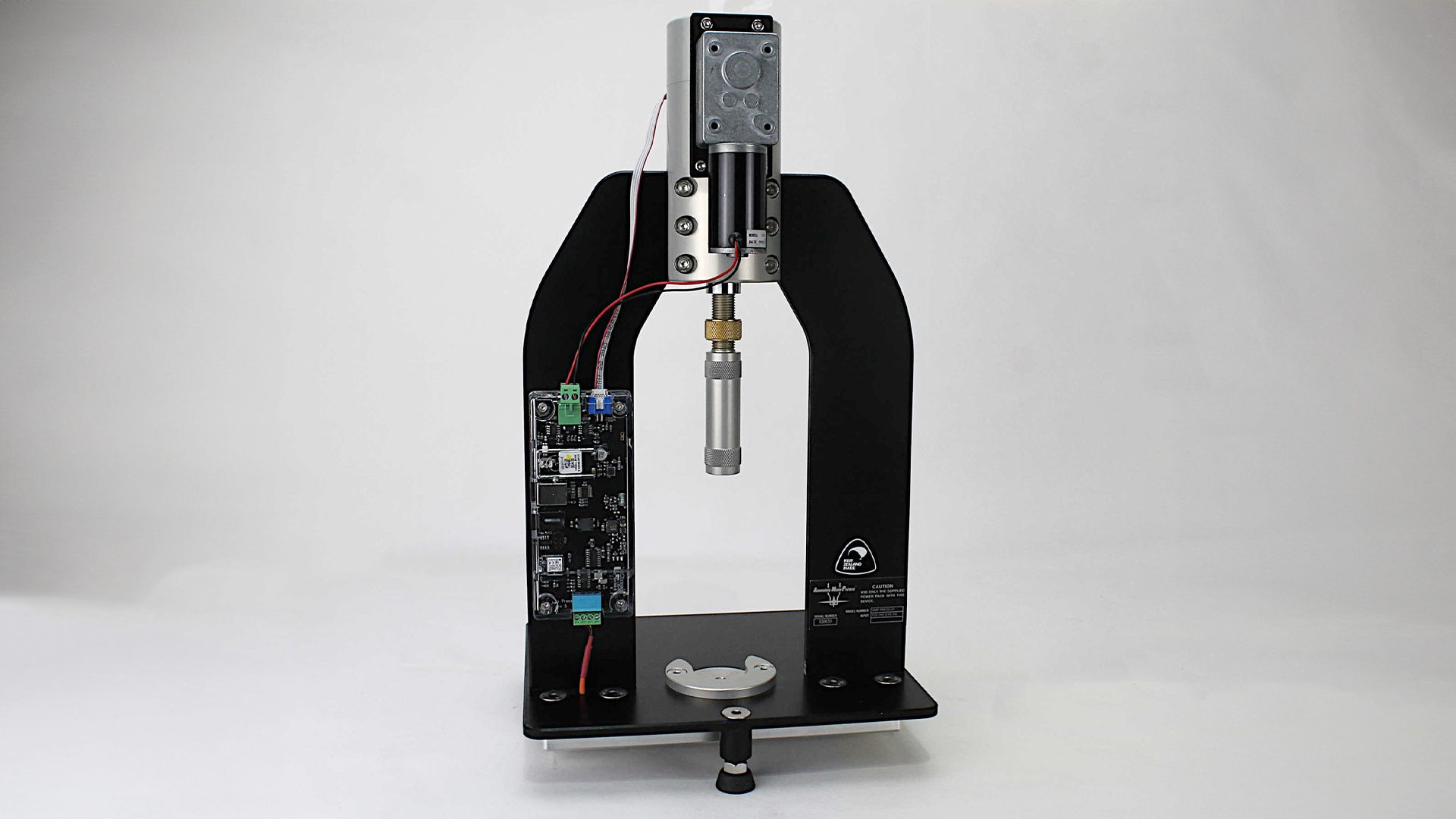
As our tools become more sophisticated, handloading’s image may be changing from one of a workbench hobby to a laboratory pursuit. A chronograph used to be beyond the reach of handloaders because the technology was unrefined, and the cost for a home unit was prohibitive. Today, we have affordable choices in optical, magnetic and Doppler radar chronographs. Powder tricklers have become “plug-n-play” devices. Powder scales went from “eyeballing” a balance beam to punching buttons on electronic units. Measuring to within +/- 0.1 grain has been the norm for decades, but available now are reloading scales 10 times more accurate, measuring down to .01 grain.
COMPUTER ON THE BENCH
Now, with its remarkable integrated press, New Zealand company Annealing Made Perfect (the same company that brought us induction case annealing) has made a quantum leap into the future—or perhaps finally brought us into the present—with the first tool on the handloader’s bench requiring a computer and software for operation. The AMP Press is basically a load cell and position sensor configured as a reloading arbor press that measures, indicates and records the force needed to seat a bullet in a cartridge case.
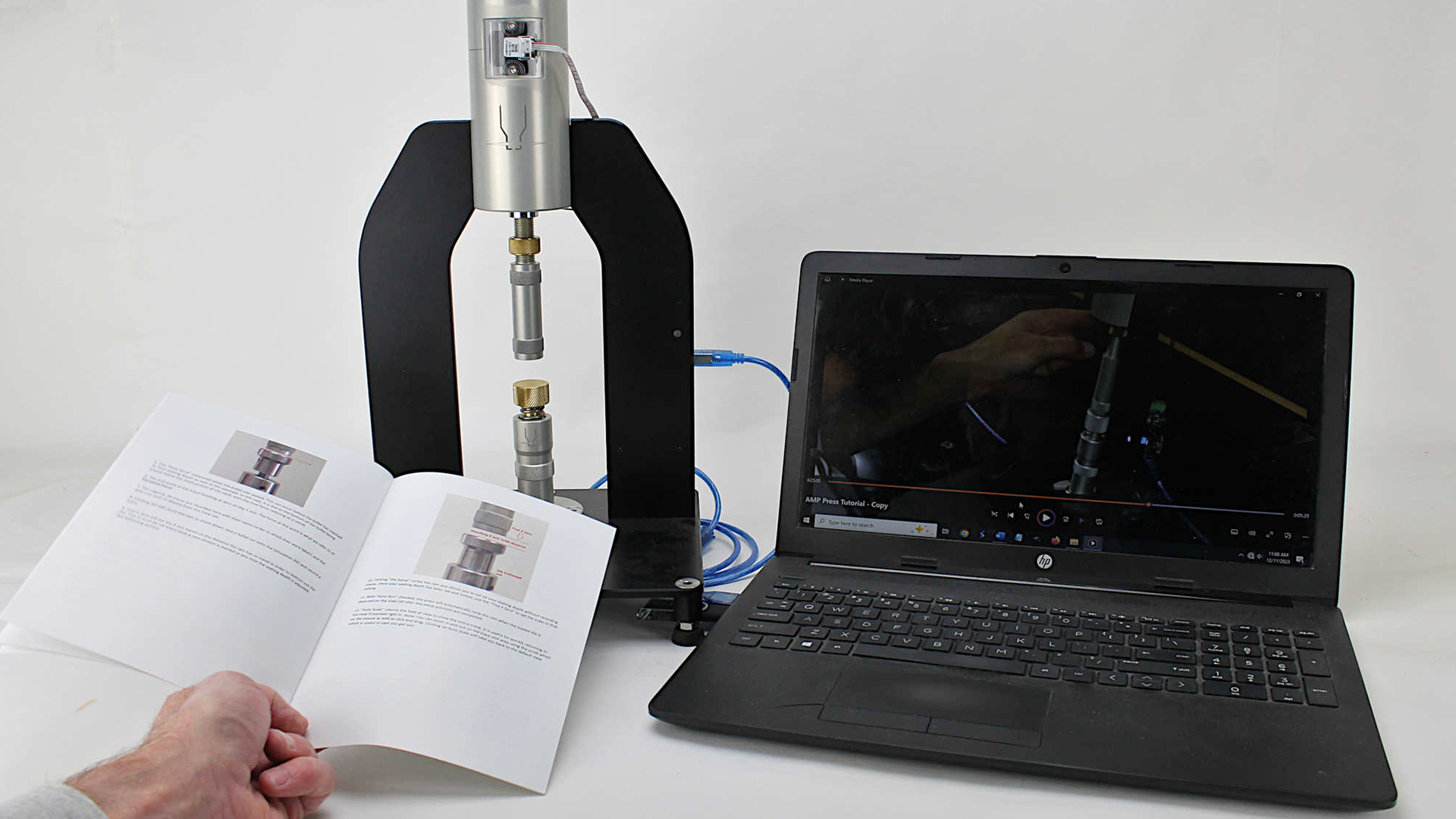
Connecting the AMP Press to a laptop or home computer via USB or Bluetooth and running the accompanying software shows handloaders exactly what’s going on with neck tension and bullet seating depth (and, by logical extension, exact case length). Neck tension is important to precision shooting, as differing tension among cartridges can widen groups and cause flyers. The AMP Press allows handloaders to cull cartridges that present any deviation from the group, aiding in preventing those exasperating unexplained flyers or widening groups.
PLOT AND TROUBLESHOOT
Setting up the AMP Press is easy, and the printed manual is augmented by instructional videos on a flash drive and more information online at the AMP website. The flash drive also has the unlock key to download the press software from AMP. Weighing about 10 pounds, the press is sturdy and nicely machined. The electronics are mounted on the back side, out of the way.
Wilson Micrometer Top Bullet Seater dies are the choice for the AMP Press, which performs only the bullet seating—case resizing and other operations are still the venue of your standard reloading press. Place a bullet on the case mouth, insert the cartridge into the die, place the die and the Wilson bullet seater base on the load cell and push the button. The motor drives the ram downward to push the seating stem and the bullet to the adjusted depth. The position sensor measuring the seating depth is accurate to within 0.001 inch.
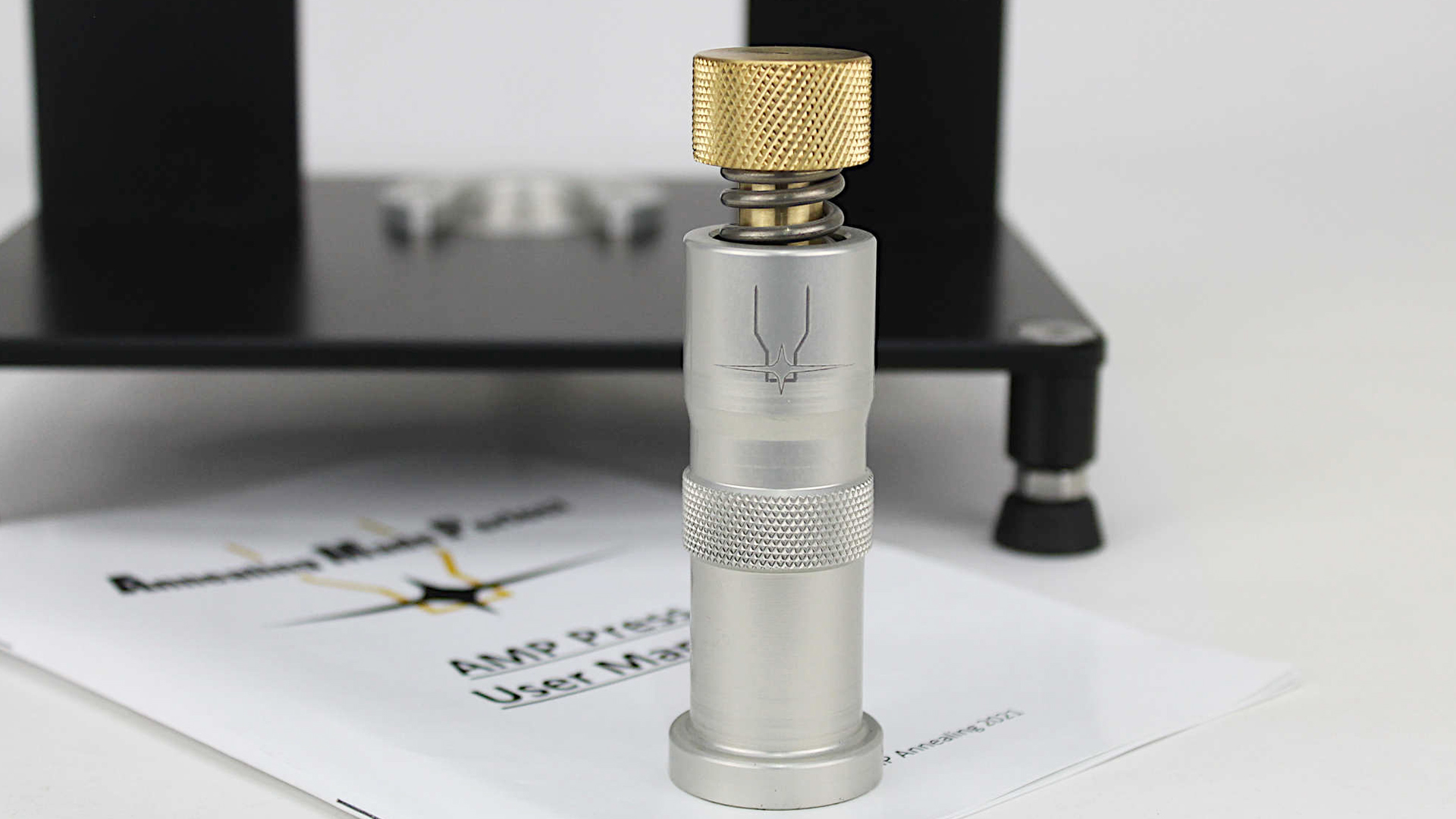
On the computer screen, a simple X- and Y-axis graph shows the amount of force (in pounds or kilograms) applied to seat the bullet, and the distance (in inches or milligrams) the ram travelled to seat the bullet (seating depth). The graph’s plot line displays the force that is required to seat the bullet from start to completion. Beyond assuring consistent neck tension, it can help troubleshoot problems associated with case neck diameter (interference fit) and condition, such as carbon, corrosion, damage or a “donut” building up inside the neck. The seating depth plot also serves as a precision indicator of cartridge overall length. Because the Wilson seater stem does not contact the bullet’s nose, variations in seating depth from case to case can be attributed to variations in case length or case head irregularity.
LEARNING CURVE
While the operation itself is quick, what does take time is learning how to understand and use the software program; it isn’t as complex and frustrating as, say, Excel or Quickbooks, but there is some learning curve. The payoff is especially sweet for the left-brained handloader, as the user can store and sort data in different ways and create cartridge profiles to see if anything changes in cartridge performance over time and multiple reloads. AMP provides a handy spring-loaded “simulation die” for learning the software and understand the results while practicing the process. And when it’s time to load, two different length rams accommodate multiple case and cartridge lengths.
At risk of sounding like marketing language, with its Annealing Made Perfect induction annealing machine and now the AMP Press, AMP continues to lead digital technology at the cutting edge of precision reloading. The AMP Press can be ordered directly from AMP for $1,395.