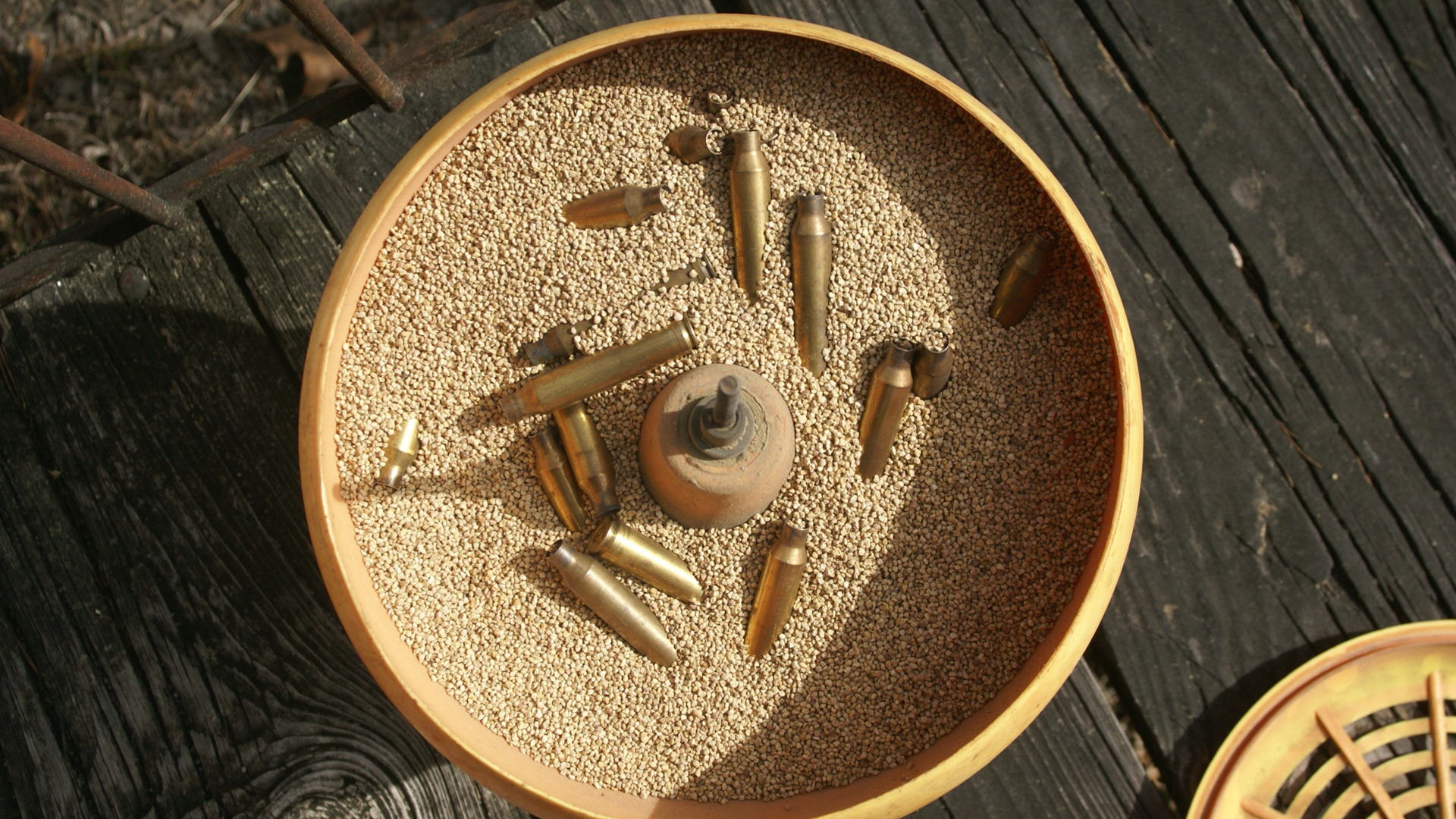
This most recent ammunition shortage—one of several that have occurred over the past few decades—has prompted some shooters to ask, “Should I become a reloader?” The answer is, “Why not?” Although the current ammo crunch has also severely impacted the availability of components, that will change as it did during previous shortages. Shooters who have become reloaders will then be able to prepare for the next shortage. It’s not that hard to do.
Reloading small-arms ammunition is a simple mechanical process that takes a fired case, re-conforms it and installs the necessary components to make it ready to fire again. Properly reloaded ammunition can be as reliable and accurate as factory rounds, if not more so—and much less expensive.
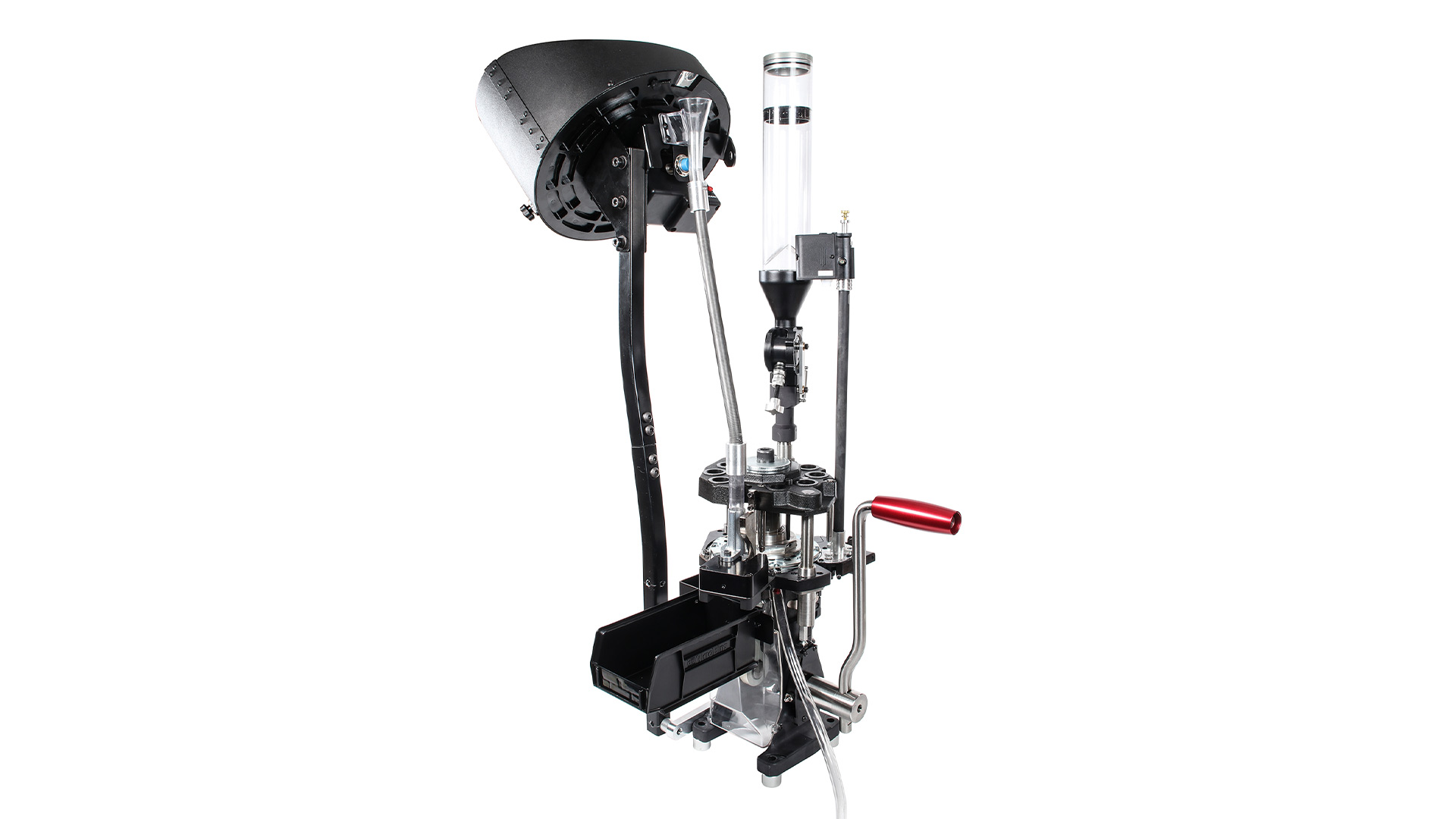
It takes a variety of tools to reload rounds, but they are not as complex or expensive as some might think. Careful online shopping can shave 10 to 20 percent off the manufacturer’s listed price. Here’s how to start reloading ammunition without spending a fortune.
An important, but sometimes overlooked, first step is cleaning the cases. Dirty range brass will gum up the reloading dies. A number of methods to clean brass cases exist, but the least expensive is a tumbler with media. My 20-year-old Lyman Turbo Tumbler, with a mix of walnut and corn cob media, will clean 500-plus cases in about three hours. The tumbler and enough media for thousands of cases can be had online for about $75, and additional media is not expensive. The drawback is that they do produce some dust, so running the tumbler on the back porch or garage is a good idea.
Reloading dies do the actual case forming, bullet seating and crimping. A die set will run $35 to $60 online. Handgun dies are not necessarily limited to one specific round. There is enough adjustment to allow .38 Spl./.357 Mag. dies to load both. The same holds true for .40 S&W/10 mm, .45 ACP/.45 GAP, and .44 Mag./.44 Spl. In addition, dies for straight-walled handgun cartridges are available in three- and four-die sets.
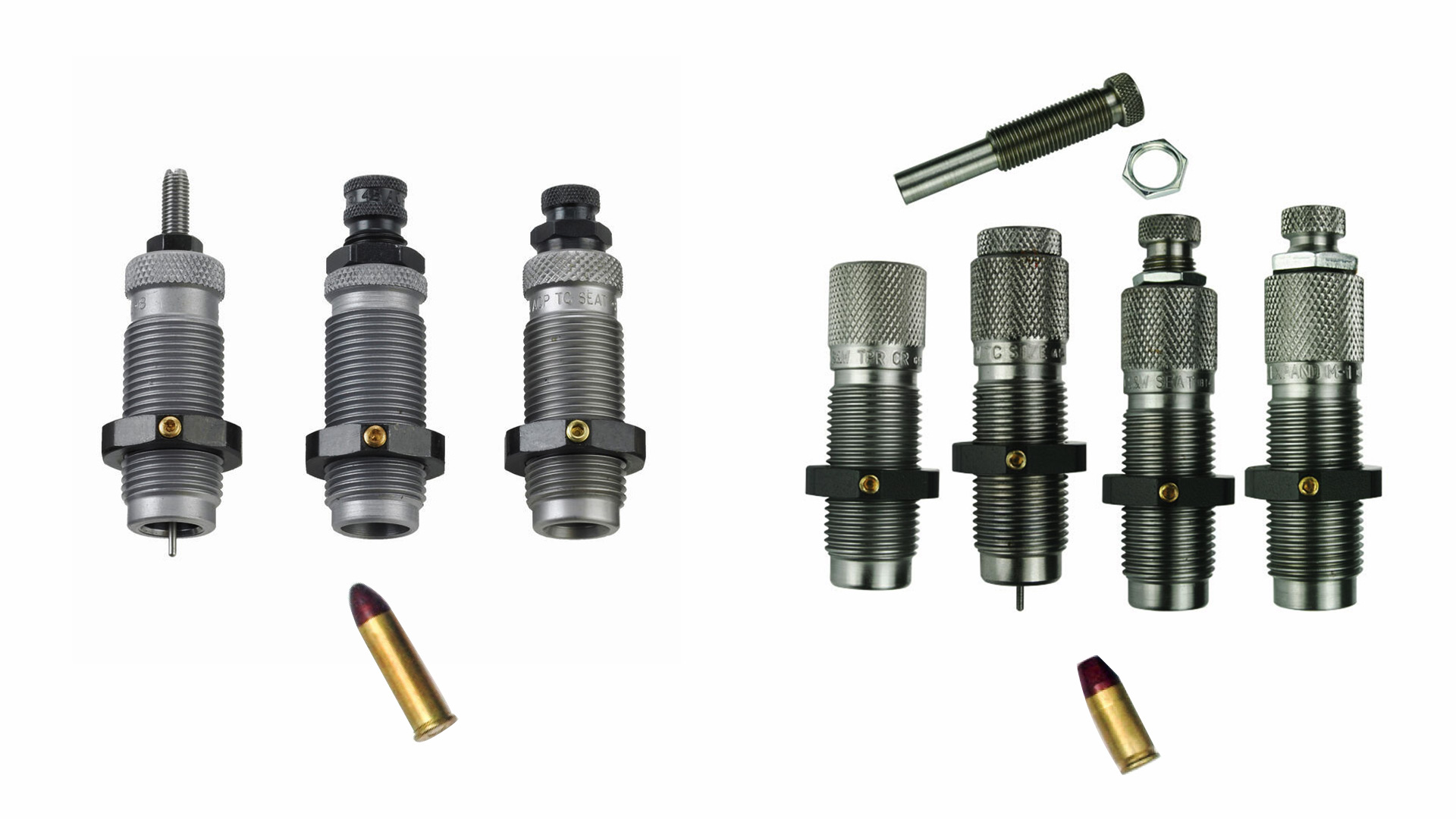
Three-die sets are commonly used for revolvers. The first die re-sizes and de-primes the case, the second die bells it, and the third die seats and roll-crimps the bullet. Semi-automatic cartridges require a taper crimp, and that die is added in the four-die sets. When reloading .38 Spl. match rounds, I prefer a taper crimp. A separate tamper crimp die is available, but my 9 mm taper crimp die easily adjusts for that. These die sets are available in plain steel or with a tungsten-carbide insert. Plain steel dies require the cases be lubricated prior to sizing and cleaned afterwards. Using the carbide dies eliminates that time-consuming step. Although carbide dies cost a few bucks more, they’re worth the additional expense.
Dies for bottleneck rifle cartridges are two-die plain steel sets. The first de-primes and re-sizes. Belling is not required, so the second seats the bullet. Tungsten carbide is not an option for bottleneck cartridges and case lubing before re-sizing is required. There are several ways to accomplish that, but one quick way is to toss a bunch onto a cookie sheet and spray them with Hornady OneShot or RCBS Case Slick spray lube. These sprays don’t risk deactivating primer or powder, but a quick wipe with a rag after sizing is recommended.
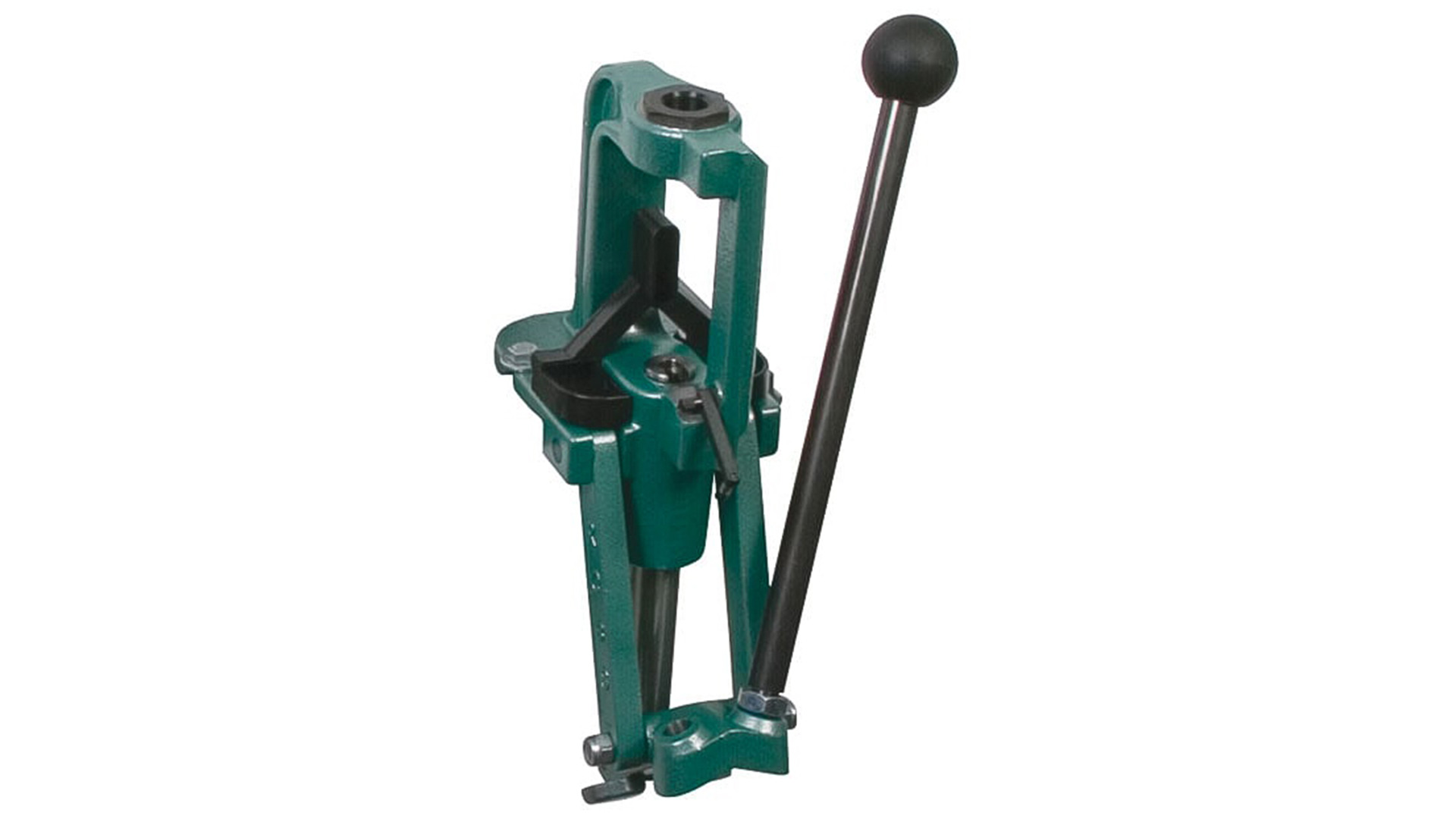
A reloading press is required to provide the leverage that make the dies work. There are two basic types: progressive and single stage.
A fully assembled progressive press will have all the dies installed, along with priming tool, powder drop and some include a bullet drop. A case is fed into the first station and when that operation is completed it rotates to the next station, and another case is inserted into the first station. Once all stations are full, a loaded round will drop out with each pull of the handle. A fully assembled progressive press will run anywhere from $850 to over $3,000.
The advantage to a progressive press is the ability to crank out more than 500 rounds per hour. The disadvantage (other than cost) is that there is minimal opportunity to inspect each round during the process. It is not hard to miss a case that splits on resizing, a neck split on belling, an inverted or missed primer or a missed powder charge. Experienced users of these presses will carefully inspect each finished round and will even put them through a case checker or plunk test them in their barrel. This adds time.
A single-stage press performs one operation at a time with one die installed. A quality single-stage press will run in the $100 to $200 range. The advantage (other than cost) is that each case receives two inspections on each step—when inserted and when removed after the operation. There’s little chance of a botched case slipping through. This can be especially important for new reloaders and will greatly assist them in turning out quality loads.
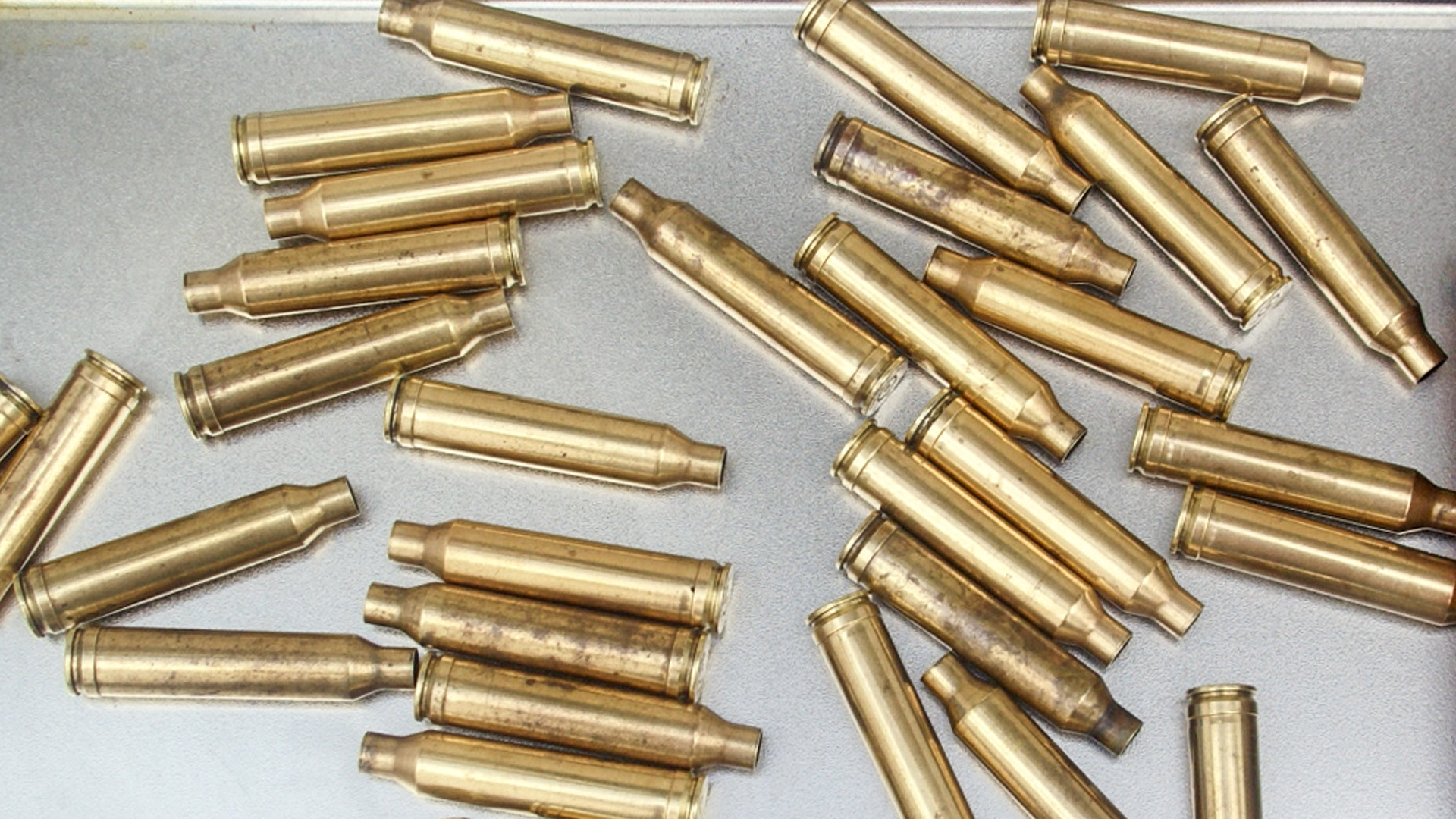
Single-stage presses are obviously much slower than a progressive press, and 500 rounds per hour is not possible. But if reloaders use the batch processing method, they can create the rounds they need within a reasonable period of time. For example, it takes me about an hour to resize and de-prime 500-plus cases on my RCBS Rock Chucker. Belling them takes less time.
With the cases properly prepared, priming, powder charging and seating the bullet are the final steps. We’ll discuss those in Part Two.
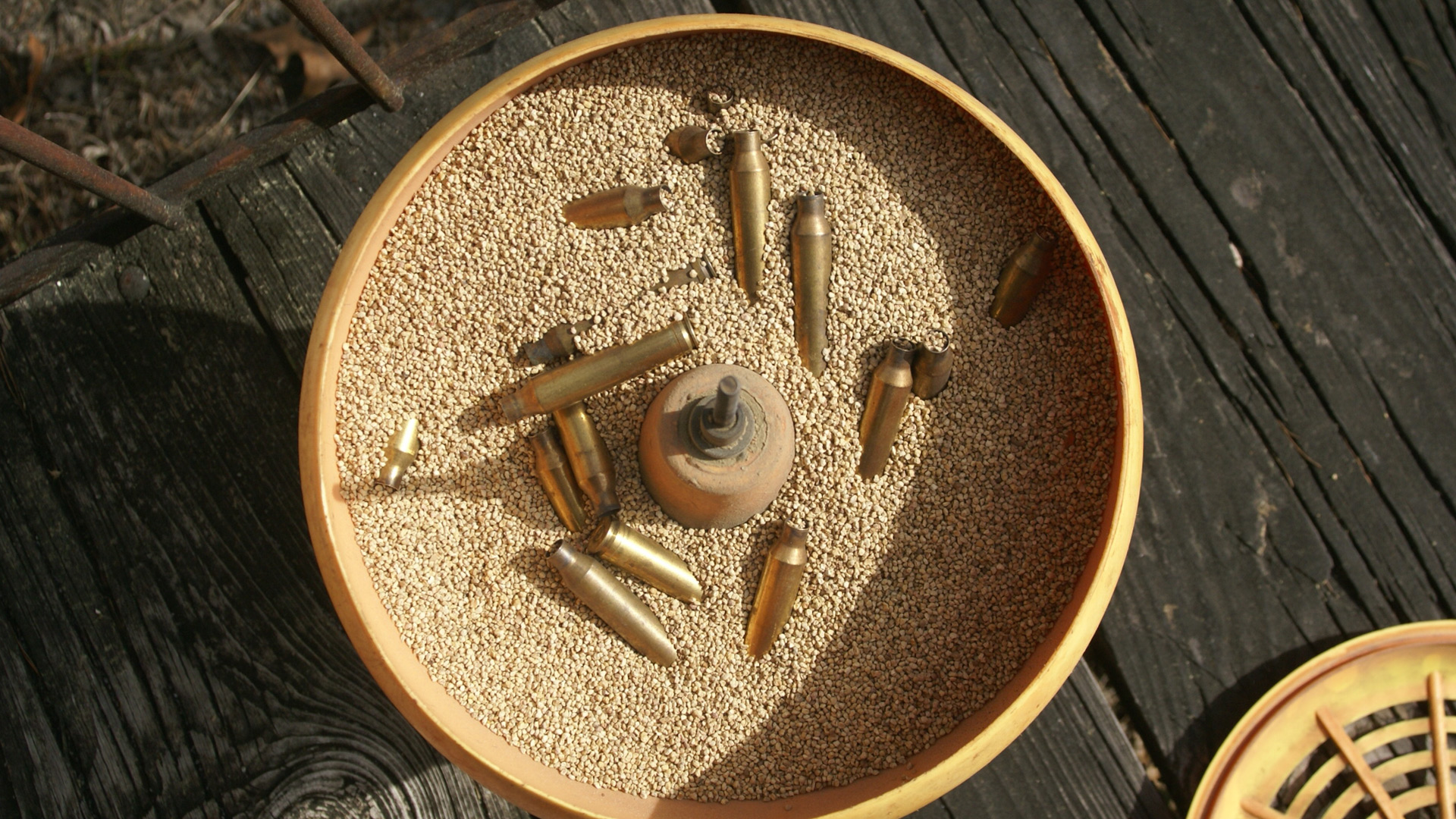
Photo: A simple tumbler with media is an inexpensive, yet effective, way to clean brass before resizing.
Read more: Surviving The Ammo Shortage