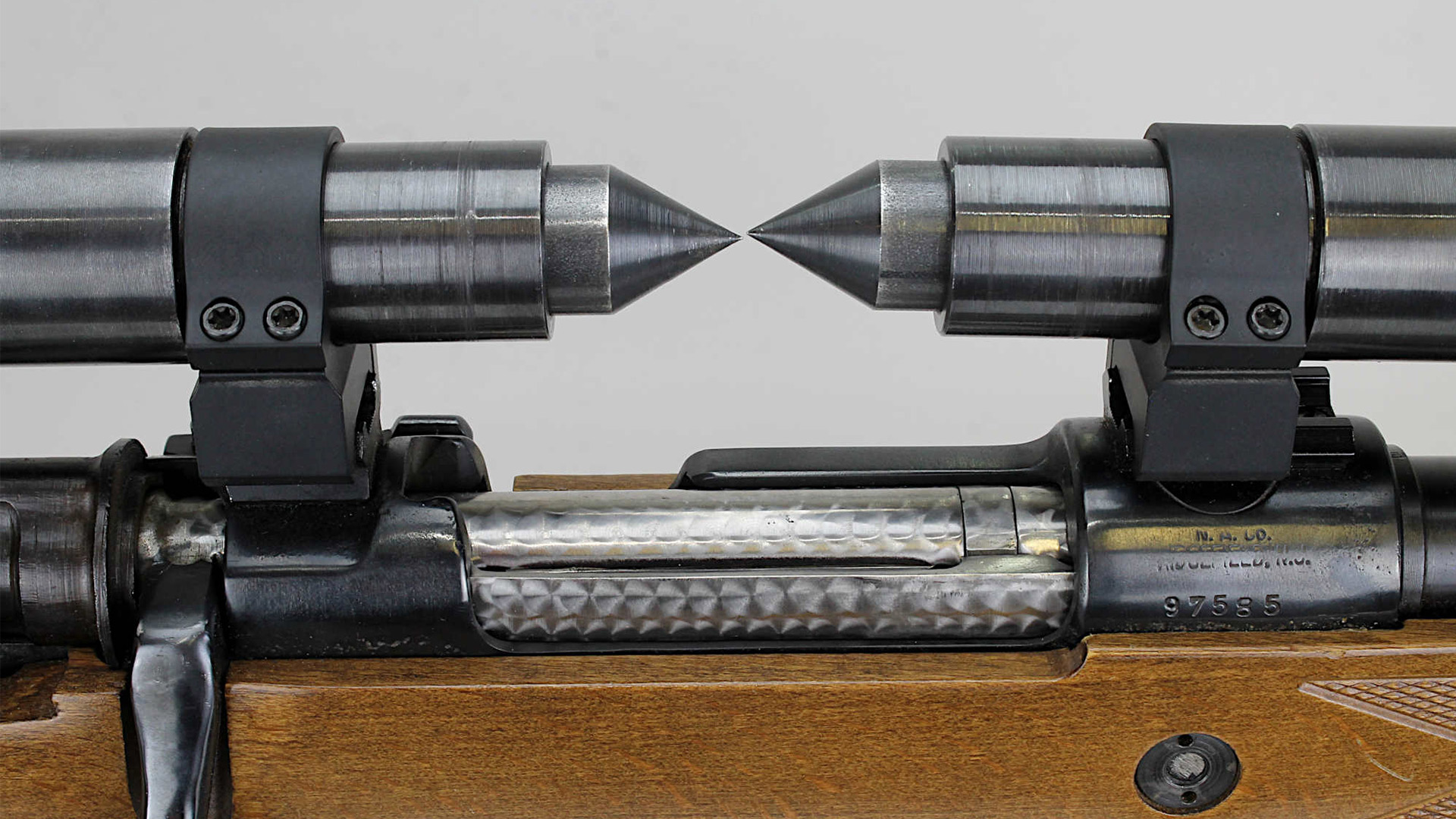
Mounting optics or repairing the mistakes of DIYers constitutes a significant portion of employment for many general-work gunsmith shops. Here’s a quick list with six of the most common optics mounting errors that can land your firearm on the gunsmith’s bench.
Using the wrong tools
Many manufacturers have moved away from slotted screws for scope mounting, instead favoring Allen or Torx types. Using ill-fitting tools of these types—say a metric Allen wrench on an Imperial-size head that seems “close enough” in size—typically results in stripping the head receptacle. Slotted screws are still abundant, and only hollow-ground screwdrivers of proper fit should be used on gun screws. Using the wrong size blade or an automotive type screwdriver on these can damage the screw heads—and if overtightened, often ruins the slot completely upon attempting removal. A torque wrench also numbers among proper tools for scope mounting, addressed below.
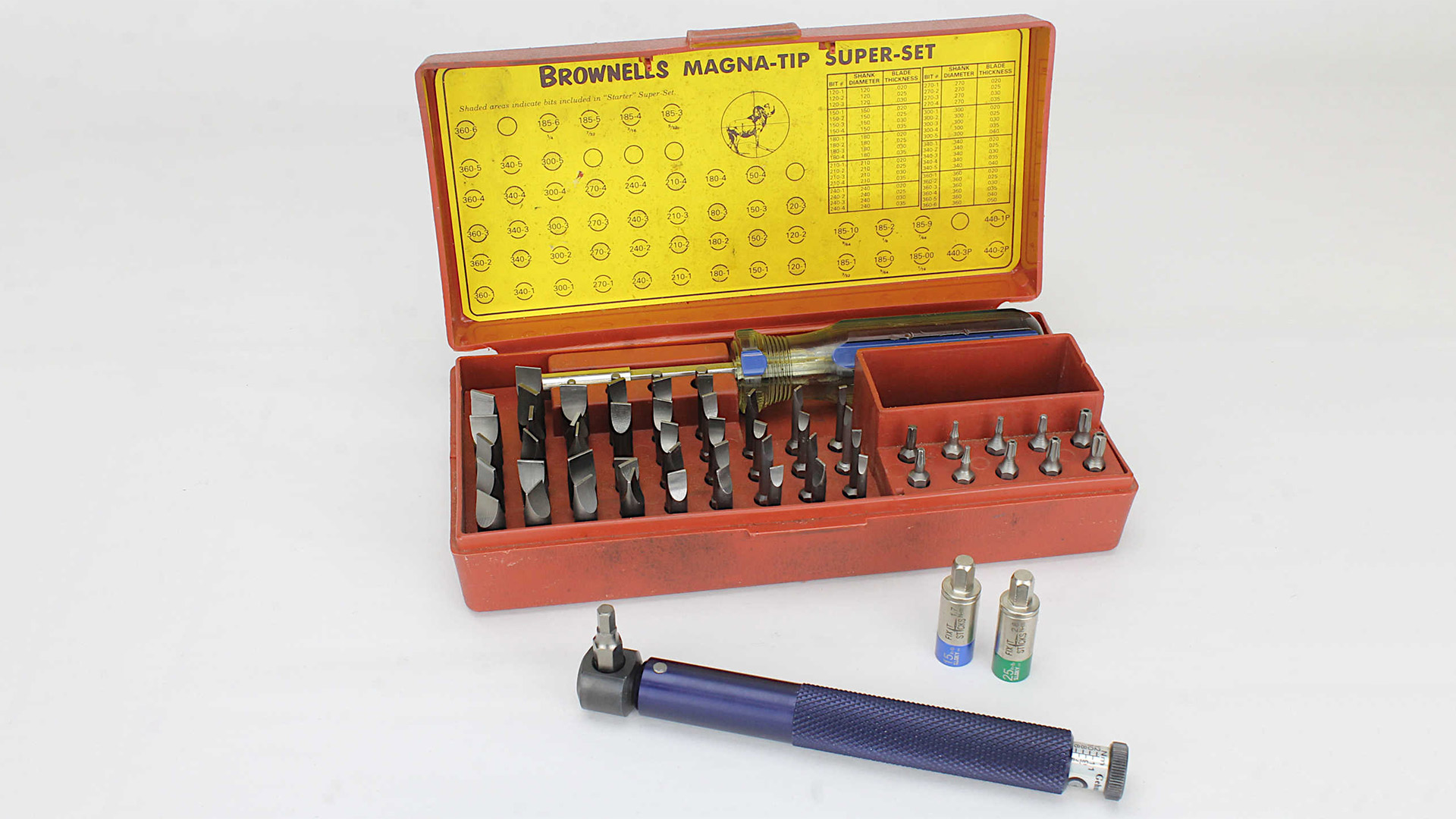
Overtightening ring and base screws
This is the most common error in scope mounting. Overtightening results in snapped-off screws or stripped threads, and sometimes screw heads so damaged upon attempting removal that they are not reusable and may require drilling out. Ring and base screws need surprisingly little tightening; for most rifles, ring screws need be torqued to only 15 to 17 inch-pounds and base screws only 14 inch-pounds, or perhaps 20 inch-pounds for magnum rifles. Specific mount systems will deviate from this general rule, such as with Leupold’s Mark 4 style rings, for which the maker recommends 65 inch-pounds of torque, and screws/nuts holding optics to Picatinny or Weaver rails (about 20 to 25 inch-pounds) but the above values apply, again, to most optics mounting.
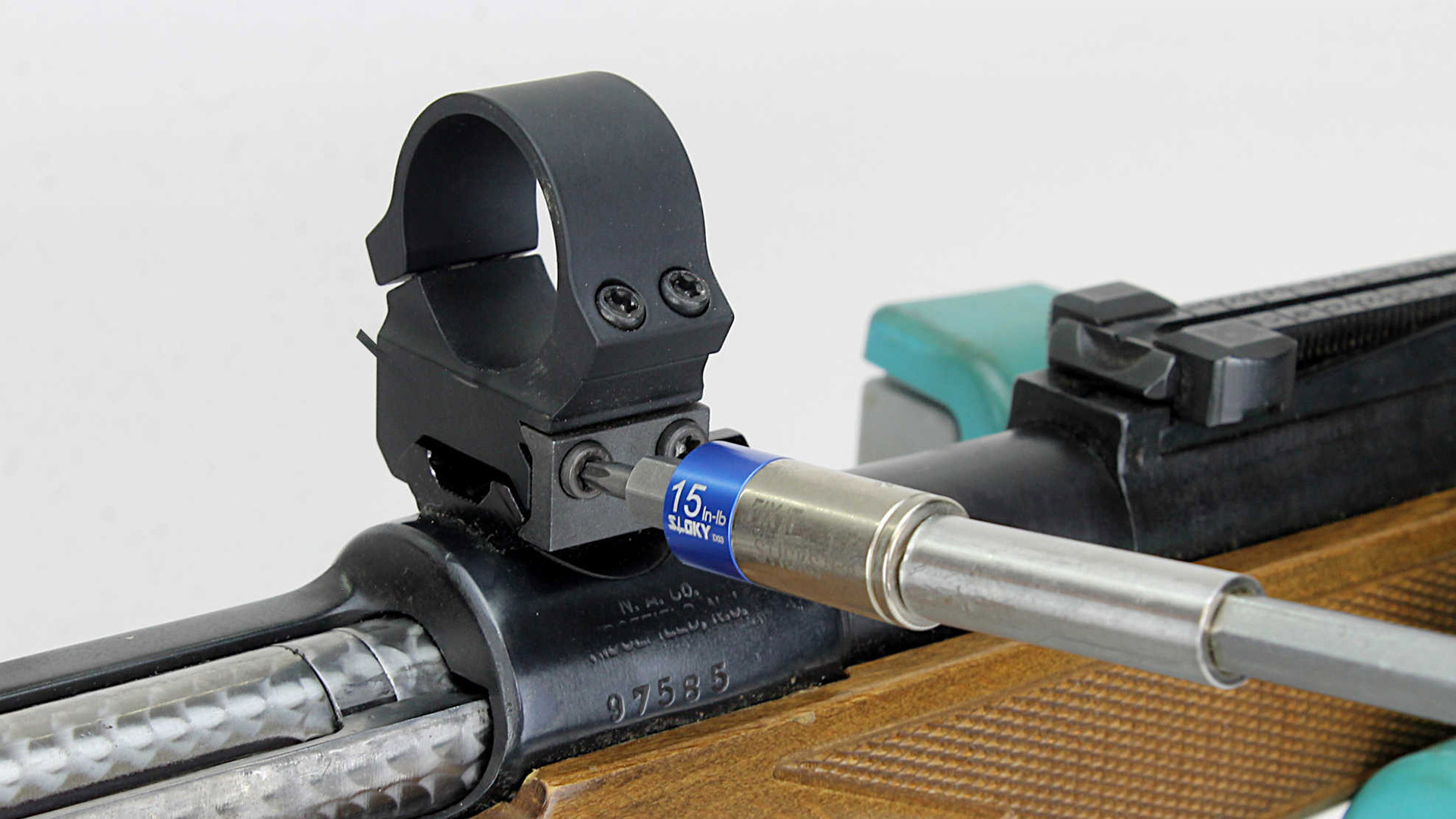
Thread locker on ring screws
For most rifles, thread locker—brand name “Loctite” for example—is not necessary on ring and base screws. Only the heaviest-recoiling rifles might justify thread locker on base screws, and then it should only be the blue, removable type. The red type is for permanently locking screws; combine red thread locker with overtightened screws, and when it comes time to remove a scope and bases, you’ve got a problem.
Rings not aligned
Rings out of alignment with each other applies unnecessary bending stress to the scope tube, which can affect its internal working parts and seals. Especially important to long-range competition rifles, any alignment error becomes magnified with distance, and a shooter may find an ostensible ⅛-inch windage or elevation adjustment at 100 yards becomes perhaps ⅜-inch at 600 yards and more at 1,000 yards. Alignment is checked with alignment rods, and can be adjusted with lapping, shimming and other methods. (See an example of scope ring alignment rods in the picture at the top of this article.)
Oiling rings/scope tube
It doesn’t make sense to lubricate two joining parts that you specifically don’t want to move. When rings fit properly to scope tubes, water intrusion between the two is unlikely, but cheaper ring/scope combos may not fit so well. If you feel you must have a corrosion preventative between rings and scope tube, apply a preservative type oil and then wipe it off completely with a dry cloth before assembling. There’s enough left behind to do the job.
Base screws too long
Receiver screw holes for scope bases on a great many firearms are typically drilled and tapped all the way through, into the channel where the bolt rides. Base screw length, then, is critical. It must be long enough to engage all the threads in the screw hole for proper grip, but not so long as to interfere with the movement of the bolt. Occasionally, rifles come to the shop with stiff or immovable bolts caused by a too-long screw protruding into the bolt channel.
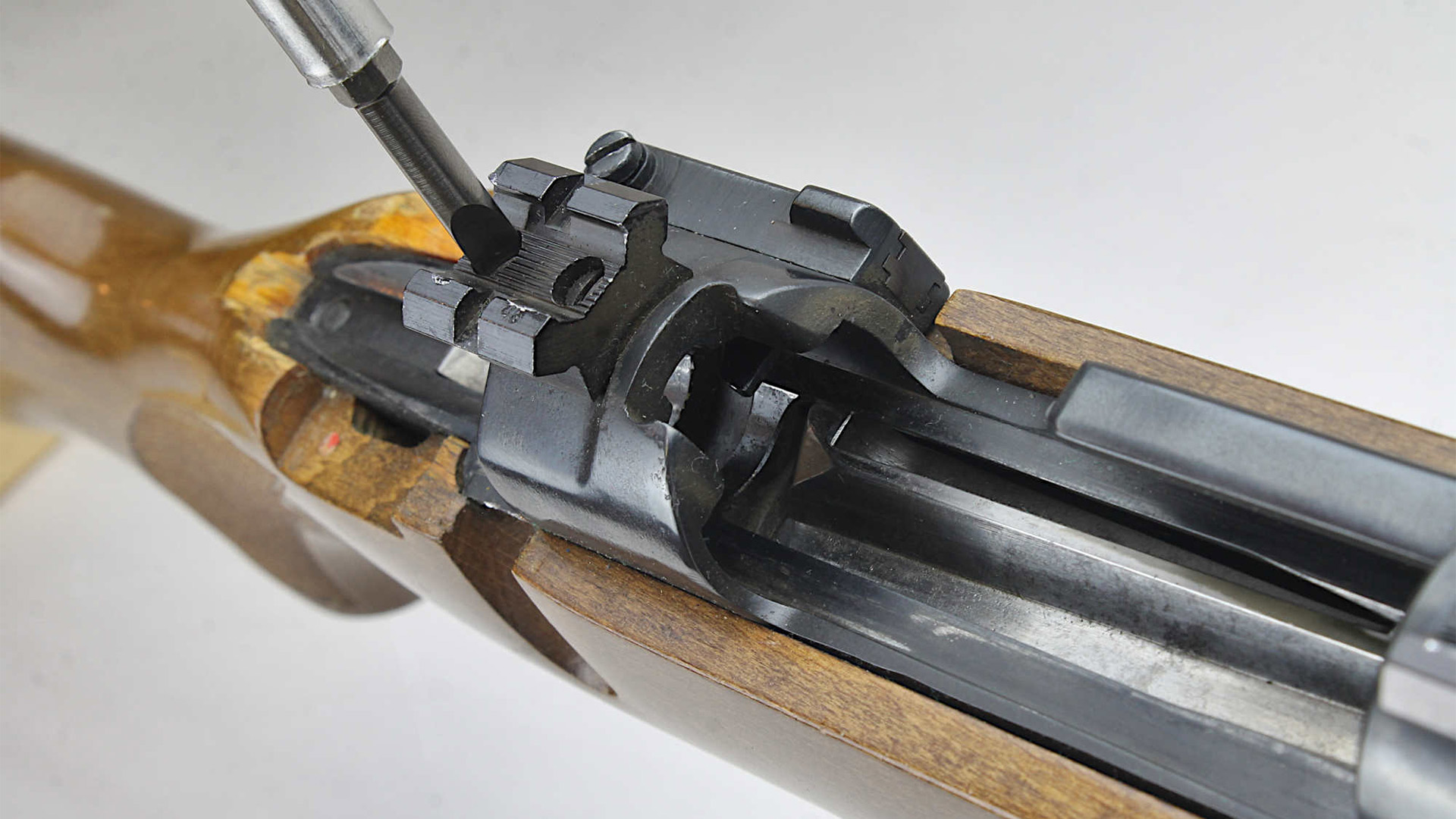
Any DIY-inclined person can properly mount optics with a bit of knowledge and the correct tools. Utilizing both can prevent frustration, problems and downtime at the gunsmith.
See more: Accuracy vs. Precision: Sharpen Your Shooting Skills