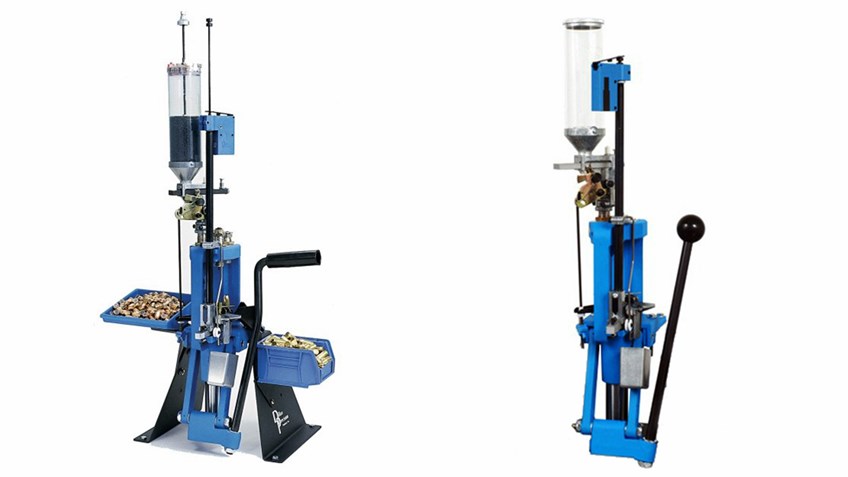
WARNING: All technical data in this publication, especially for handloading, reflect the limited experience of individuals using specific tools, products, equipment and components under specific conditions and circumstances not necessarily reported in the article and over which the National Rifle Association (NRA) has no control. The data has not otherwise been tested or verified by the NRA. The NRA, its agents, officers and employees accept no responsibility for the results obtained by persons using such data and disclaim all liability for any consequential injuries or damages.
The previous article in this two-part series discussed the proper procedures for selecting and preparing components for match-grade loads. This article will briefly present the precision reloading techniques and tools used to produce cartridges having the greatest possible uniformity, and thus accuracy, from such components.
Reloading Dies
There are basically two types of dies used to reload cartridges: the familiar ⅞-14-threaded dies used in conventional single-stage and progressive presses, and the hand dies preferred by benchresters, which are used with a small arbor press. These latter dies are often called Wilson-type dies after L.E. Wilson, who was the first to commercially popularize them.
As a general rule, more consistent ammunition can be loaded with Wilson-type dies than with standard ⅞-14 dies. Wilson-type dies are generally made to a greater level of precision. Also, the working tolerances and “spring” of standard ⅞-14 presses can introduces small inconsistencies into the sizing and bullet seating processes, producing cartridges that are not as straight or concentric as those loaded with Wilson-type hand dies.
While standard ⅞-14 dies can size only cases having standard thickness neck walls, Wilson-type dies feature interchangeable bushings that allow the shooter to size standard or turned necks to precise dimensions, for guns having tight-neck chambers that more precisely align the bullet with the bore. Among ⅞-14 die makers, Redding offers sizing dies with interchangeable neck-sizing bushings. The terms “sizing” and “resizing” are often used interchangeably.
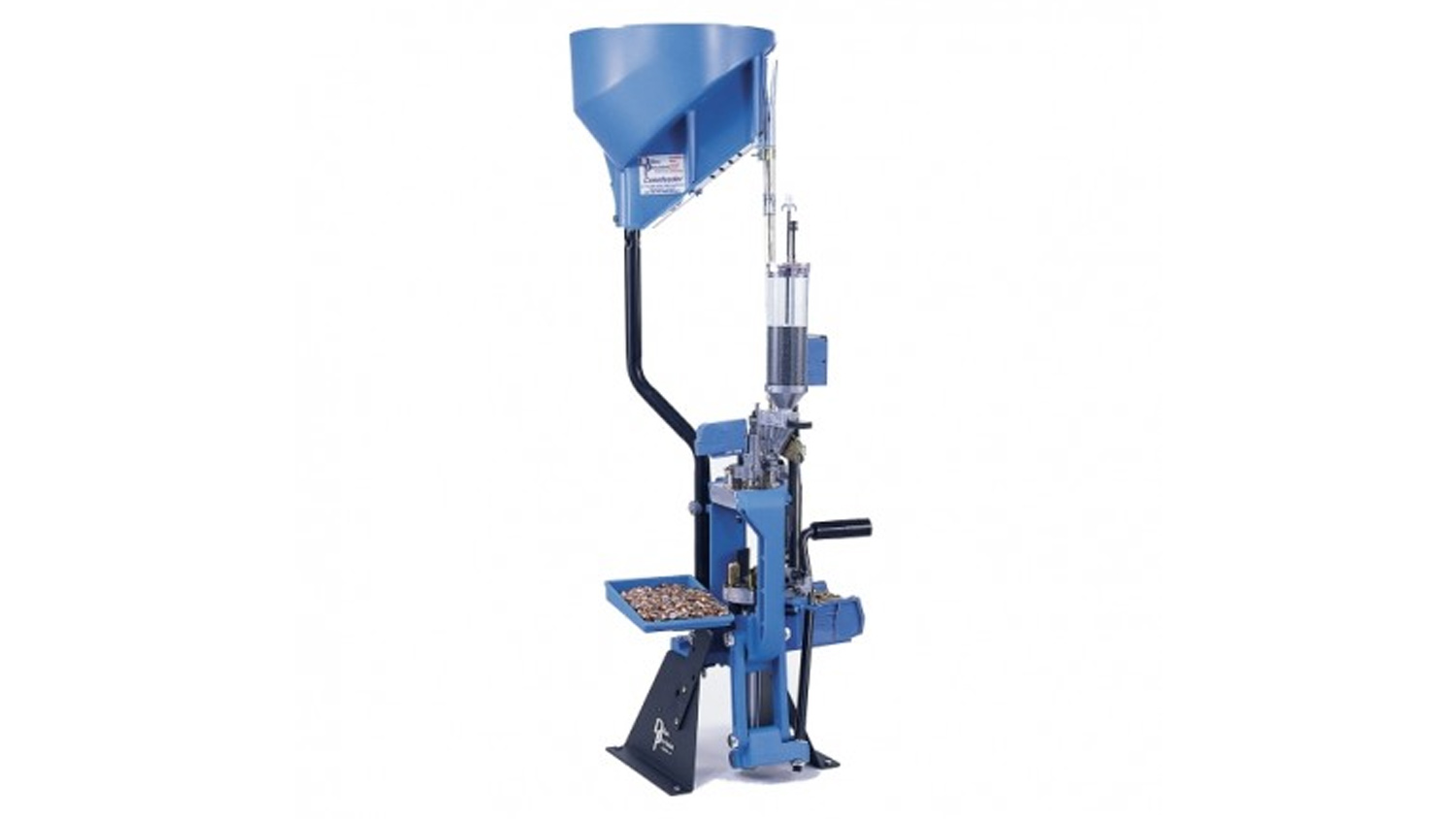
Case Sizing
When a cartridge is fired in a gun, the case first expands under pressure to seal against the walls of the chamber, then, as pressure drops, contracts slightly—enough to allow extraction—but not all the way back to its original dimensions. Before that case can be used to assemble a new cartridge, it must be sized (returned to minimum dimensions) first. The sizing type you use—full-length or neck—depends largely upon the requirements of your shooting discipline.
Full-length sizing is accomplished using a sizing die, which sizes both the case neck and the case body, and, on a bottleneck case, sets the shoulder back. The resulting sized case has a slight clearance between it and the chamber walls. Full-length sizing dies are made in both ⅞-14 and Wilson-type versions.
Shooting disciplines that require rapid reloading often utilize full-length resizing, as a fully sized case chambers more reliably. For the same reason, cases used in semi-automatic rifles that are fed from a magazine are usually full-length sized. Full-length sizing is also needed for cases that will be used in a different gun than they were originally fired in. Occasionally, virgin brass must be full-length sized to fit into a minimum-dimension chamber.
Sizing die adjustment is critical. The conventional method of setting up ⅞-14 sizing dies—screwing the die in until it just kisses the shell holder when the ram is raised—does not always produce the optimum sizing for best grouping. Sometimes it sets the shoulder back too far, which increases headspace and consequently reduces both accuracy and safety. Some authorities recommend setting the shoulder back no more than about .002 inch and less if possible. When loading for a bolt gun, for example, the case should be sized only so far as to give a sensation of slight friction during bolt turndown.
Chambering reliability in semi-auto rifles is promoted through the use of small-base, full-length sizing dies, which size the head area of the case to a slightly smaller dimension than do regular sizing dies.
Full-length sizing has some drawbacks. The case body is worked more, and may more quickly work-harden and become brittle, leading to shorter case life. Also, since cases that are full-length are slightly loose in the chamber, the do little to precisely align the bullet with the bore.
While Wilson-type dies generally produce the most uniform ammunition, good accuracy can also be obtained with standard ⅞-14 full-length sizing dies—1/2 moa or better with a high-quality press and properly adjusted dies. This is sufficient for most rifle silhouette and high power competition.
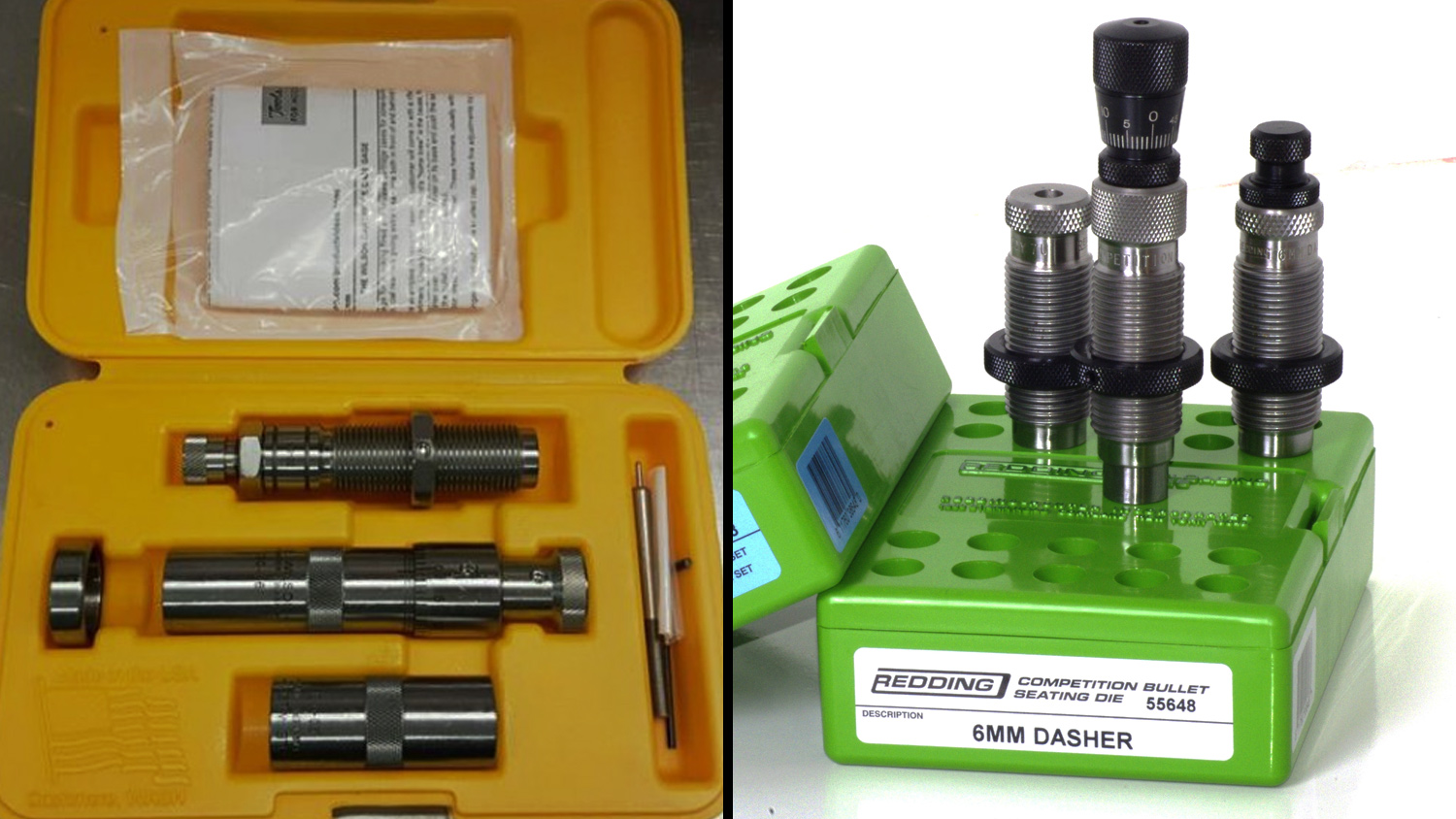
As described previously, a fired case is a close match to the chamber it was fired in, and is said to be fire-formed to that chamber. Such a case does not need to be full-length sized to be used in the same chamber; in fact, since that case is already aligned with the breechface, the chamber and the bore (assuming those gun components are themselves true), better accuracy can be obtained by only sizing the case neck. Additionally, since neck sizing causes the brass to be worked less, both in the die and in the chamber, it can extend case life.
Neck sizing is the method of choice with bolt-action rifles, particularly when they are single-loaded; however, in semi-automatic rifles, or even some repeating bolt guns, neck-sized brass is usually too tight a fit in the chamber for reliable feeding.
Special neck-sizing dies, which can be had in both standard ⅞-14 and Wilson-type versions, are often used instead of conventional full-length sizing dies. Two types of neck-sizing dies are produced: solid dies that size the neck to only one such dimension, and dies with interchangeable neck-sizing bushings allowing sizing in .001-inch increments. Neck sizing with standard ⅞-14 full-length sizing dies can also be accomplished by running the case into the die only that distance that will size the neck but not size the body or set back the shoulder.
The amount of the neck that is sized can vary; some reloaders size the entire neck, while others only size half the neck or less. My feeling is that the bullet may end up straighter in the case if the neck is sized along the bullet’s entire seating depth.
Neck Tension
Best grouping is achieved when neck tension (the grip of the neck on the bullet) is uniform; this is accomplished through careful neck turning, precise neck sizing to the proper inside diameter, and the use of highly consistent match bullets. During bullet seating, if the force required to seat a bullet is unusually high or low, the neck tension of that cartridge probably varies, and it should be set aside for practice.
Debate exists on the degree of neck tension that is best for accuracy. In years past, many benchresters used so little tension that the bullet could be pushed into the neck with easy finger pressure; long-seated bullets were thus pushed back into the neck when the contacted the rifling, ensuring consistent seating depths. This thinking evolved, to the belief that better accuracy is attained with somewhat heavier tension. In any event, cartridges that are to be used in semi-automatic rifles or repeating bolt-action rifles must utilize sufficient neck tension to prevent bullet setback during feeding. Whatever tension is appropriate, uniformity is the key to accuracy.
When standard ⅞-14 sizing dies are used with cases that are not neck-turned, final neck diameter is established primarily by the diameter of the expander ball that is pulled back through the neck as the case is withdrawn from the sizing dies. By reducing expander-ball diameter by .001 inch or so can sometimes rectify insufficient neck tension.
Redding ⅞-14 neck-sizing dies with interchangeable bushings and Wilson-type neck-sizing dies employ no expander ball; the selection of the proper neck-sizing bushing for the case’s neck wall thickness and bullet diameter serves to produce the desired degree of neck tension.
As a general rule, an inside neck diameter that is about .001 inch smaller than the bullet diameter will give an adequate degree of neck tension for single-loaded cartridges. In other shooting disciplines, especially those in which cartridges feed through a magazine, a higher degree of neck tension is desired. This can be produce by sizing the neck so its inside diameter is .002 to .003 inch smaller than the bullet diameter.
For accuracy purposes, crimping is counter indicated. Not only can a heavy crimp affect neck tension and chamber pressure in unpredictable ways; it can also deform the bullet and possibly even separate the jacket from the core. It’s better to retain the bullet by increasing neck tension than by applying a crimp.
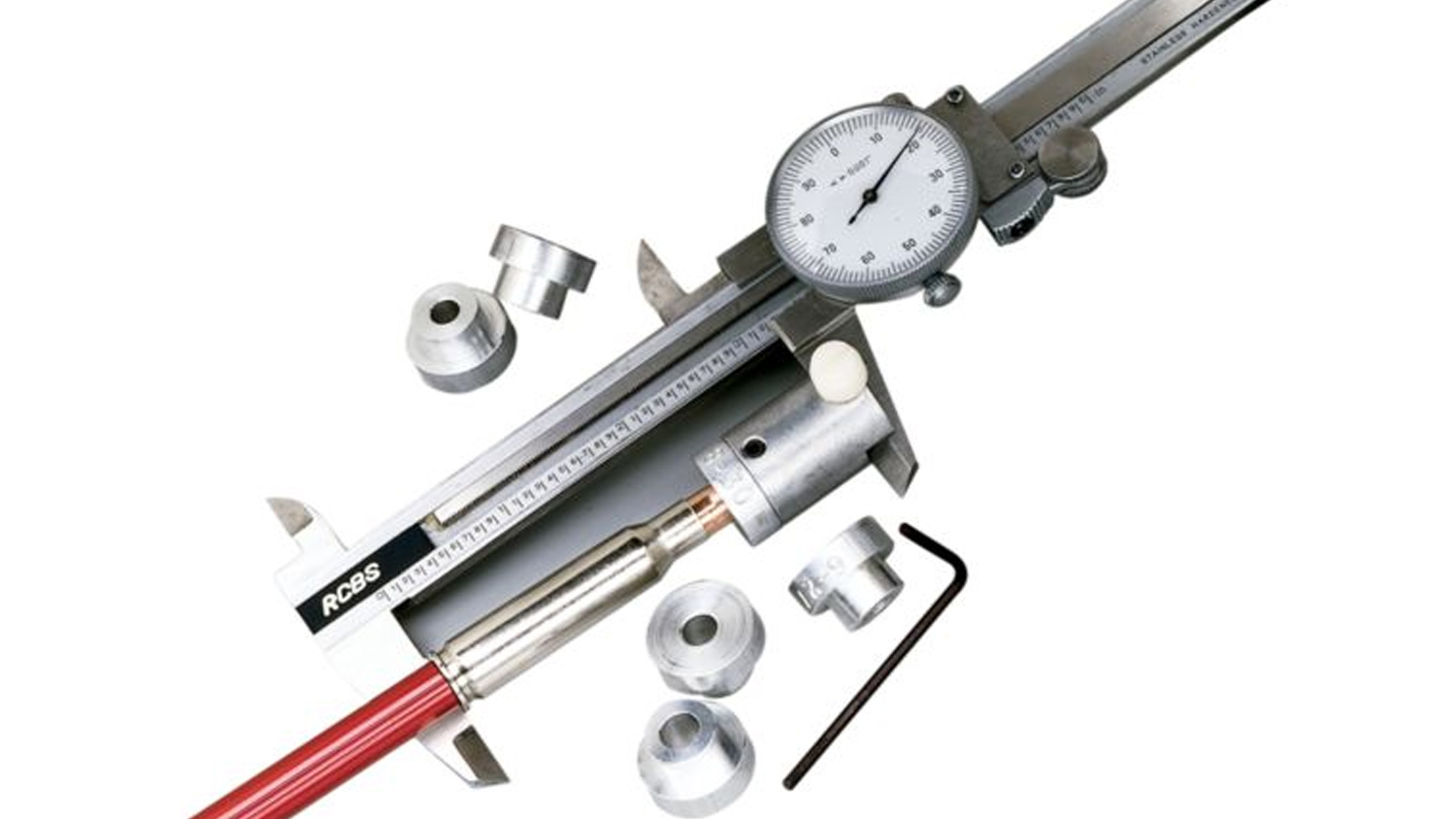
Primer Seating
Primers should be seated to the bottom of the primer pocket to give a uniform crush (compression of the primer to seat the anvil firmly against the priming compound). Most ⅞-14 presses have a priming arm that can be swung into position to prime the case on the press upstroke; however, the majority of precision reloaders use a hand-priming tool. Such a tool gives the sensitive feel required to obtain a uniform crush, and, with practice, allows a very high level of seating consistency. Primed cases in which the priming effort is unusually high or low should be put aside, and used only for practice or fouling shots.
Powder Charging
Good-quality powder measures, properly operated, can provide sufficient charge consistency (about .5 variation or less) for the most exacting reloading requirements, and are used in just about all competitive disciplines. Even among the benchrest crowd—sticklers for ultimate precision—the majority reloads with powder measures, though some purists still weigh every charge to eliminate even the few tenths of a grain variation that powder measures produce. About the only time charges must be weighed is with powders (usually slow-burning, large-grain extruded types) that fail to meter through a measure with acceptable uniformity.
A powder measure must be operated in a consistent way for the most uniform thrown charges. Some shooters recommend “bumping” the handle, or flipping a swinging knocker attached to the measure, at both the beginning and end of the stroke on the theory that this dislodges any stuck powder grains. In actual tests, however, these actions did not increase the consistency of the charges thrown. The best technique is to work the handle with the same slow, uniform stroke for each charge.
Bullet Seating
For best accuracy, a bullet must be seated straight and to the proper depth. Straight bullet seating is accomplished primarily through the design and manufacture of the dies. Again, the precision of the Wilson-type dies tends to give them the edge over standard ⅞-14 seating dies, though some of the latter type have design features, such as floating seating stems, that contribute to straight seating.
Proper seating depth (the distance the bullet is pushed into the case neck) is also important for best accuracy. Seating depth depends upon the relationship of the bullet ogive to the throat. With two bullets having the same length but different ogives, at the same cartridge overall length (OAL), one bullet may touch the rifling while the other sits .010 to .020 inch or more away. So every time you change bullet brands, even if the bullet has the same diameter, weight and design, you must readjust your seating depth.
Generally, the less “jump” from the neck to the rifling, the straighter the bullet enters the bore, and the greater the accuracy potential. Thus, best grouping is most often achieved with the bullet seated anywhere from .010 to .012 inch away from the rifling to firmly touching the rifling. Some rifles will group well with the bullets seated as much as .030 inch from the throat. The optimal seating depth for a specific gun and load is normally established through trial and error, using cartridges with their bullets seated at different depths (from touching the rifling to about .015 to .020 inch back), which are fired for group.
A quick and dirty way to establish the depth at which the bullet just touches the rifling is to load a dummy round with the bullet seated well out, smoke the bullet using a candle or match flame, and try to chamber the dummy round. Marks will appear where the bullet hits the rifling. Seat the bullet progressively deeper until the dummy cartridge chambers and just the faintest rifling marks are visible on the smoked bullet. This is your zero point; adjust your seating die from this seating depth. Competition seating dies are available with micrometer adjustments allowing control of seating depth in .001-inch increments.
Never adjust seating depth by measuring cartridge OAL. The tips of bullets of the same brand, type, lot and even bullets in the same box can differ such as to cause significant variance in OAL.
Bullet ogives may also differ, even within the same bullet lot, causing variations in seating depth. Separating bullets of different ogives can be done with a bullet comparator, which allows the measurement from the bullet base to a point on the ogive having a certain diameter. When that distance varies, it is an indication of non-uniform ogive.
Cartridge gauges that work on the same principle (measuring the distance from the case head to a point of specific diameter on the seated bullet) can be used to get an approximation of seating depth. It is only an approximation, however, as comparators do not precisely replicate the throat diameter or throat angle of your chamber. Seating depth is thus a fairly complex issue; without special tools, you are probably best off using a trial-and-error method similar to the one described above.
With maximum or near-maximum loads, pressure may climb to dangerous levels when bullets are seated out to touch the rifling. High pressure may also result when a maximum load is developed with the bullets seated well out, and then the bullets are seated significantly deeper into the case, as when a load developed in a long-throated rifle is used in a short-throated gun. In both cases, reduce the powder charge weight by 10 percent for safety.
Note that, in disciplines in which rounds must be fed into the chamber through a magazine, the magazine length often determines the cartridge OAL, and thus the bullet-seating depth. In those cases, all that can be done is to seat the bullet out as far as the magazine allows.
Case and Cartridge Straightness
Again, for top accuracy the bullet must enter the throat and the rifling dead straight. Straightness deviations often occur during reloading, due to die manufacturing tolerances (particularly a misaligned expander ball), press misalignment, or improper reloading technique. Loaded cartridges can become misaligned through being dropped, handled roughly or chambered improperly.
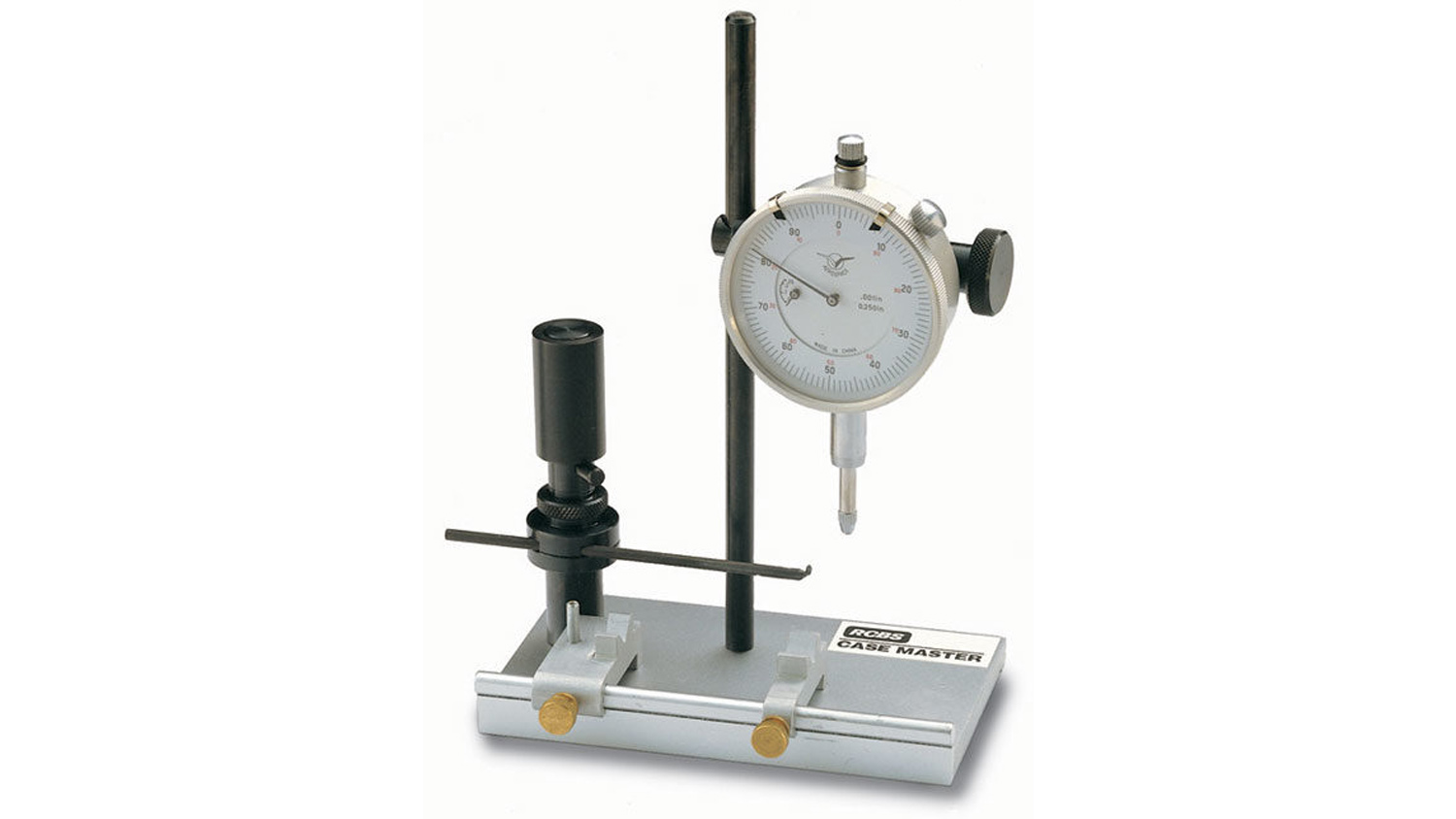
Deviations in straightness can be detected with a concentricity gauge, such as from RCBS, NECO, Sinclair and others. In most such gauges, the cartridge is placed on V-blocks and rotated slowly with the tip of a dial indicator touching at various points to detect any crookedness, wobble or concentricity defect, such as slightly banana-shaped cases. These gauges can additionally be used to measure variations in bullets and empty cases; some models also allow measurement of neck and case wall variation, and case head squareness.
Most standard ⅞-14 dies will produce about .004 inch of loaded cartridge runout with cases that have not been neck turned, and even less when neck-turned cases are used. Wilson-style neck and seating dies can easily produce cartridges with .001 inch runout, and usually a lot less. Up to about .001-inch runout is adequate for reloads used in high power or varmint rifles; benchrest shooting requires cartridges with considerably less than that level.
Testing Your Loads
Shooting is, of course, the ultimate test of any load. Both bench testing, using a rock-solid bench with stable front and rear bags, as well as testing using the actual positions that will be employed in a match or in the field, are important. If possible, fire at the same ranges, and even under the same conditions or temperature, humidity and even altitude you’ll confront in competition or hunting. A maximum load developed in 40-degree spring weather but fired on a 95-degree summer day likely will group differently and may also develop excessive chamber pressure.
Finally, chronograph the load. This is the only way to ascertain its velocity and ballistic uniformity, which in turn determine trajectory and accuracy.
Though many of the reloading procedures that have been described here were pioneered by benchresters, they are applicable to a wide range of shooting activities. However, the accuracy-enhancing potential of many of these techniques will be realized only in highly specialized rifles. The intelligent reloader will choose only those reloading techniques that are appropriate to the accuracy potential of his or her rifle and the accuracy requirements of his or her shooting activity.