** When you buy products through the links on our site, we may earn a commission that supports NRA's mission to protect, preserve and defend the Second Amendment. **
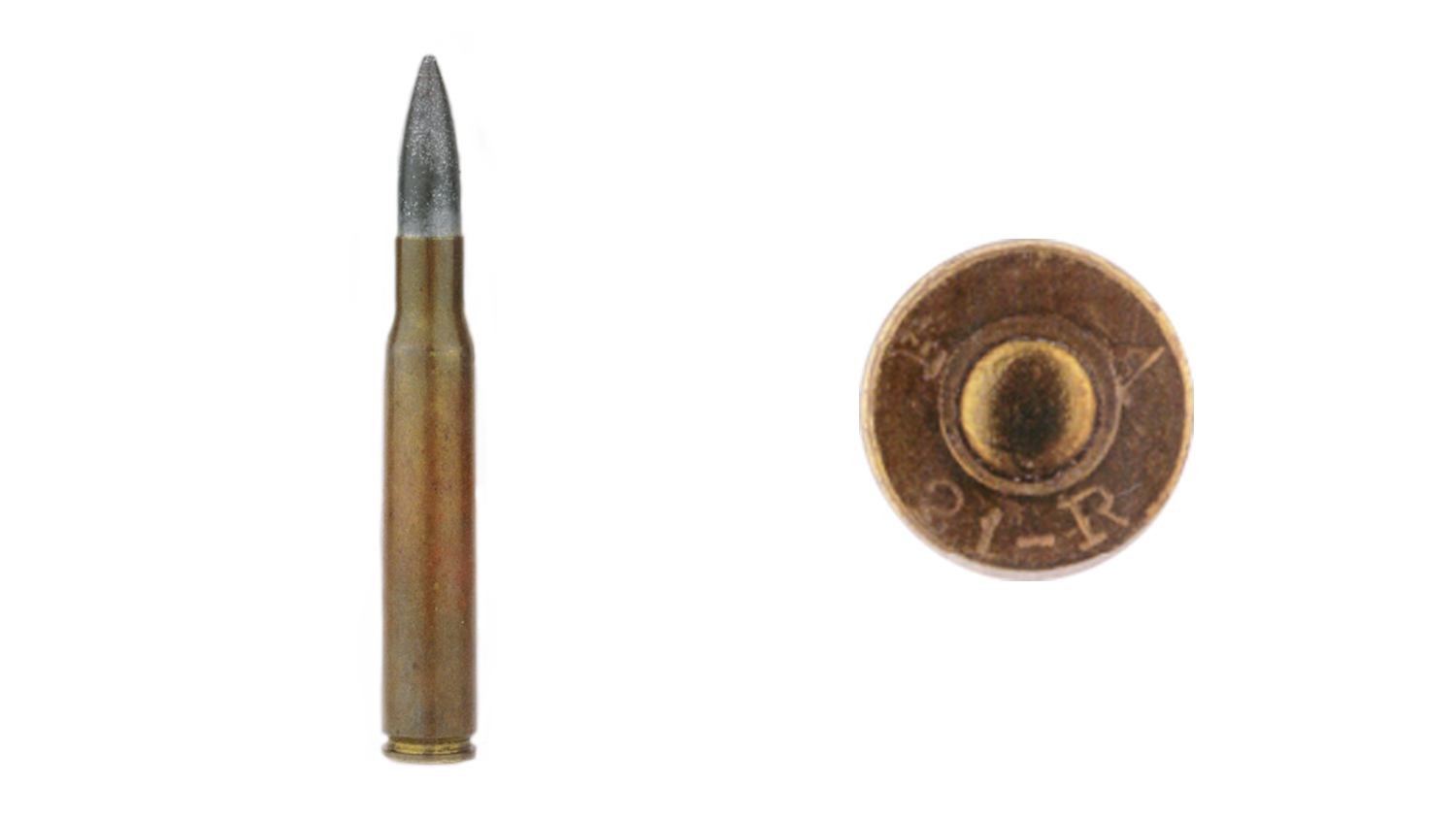
The National Matches have been, almost from the beginning, a place for experimenters, and the years following World War I were no exception. Individual experimenters measured and gauged and checked, trying to find ways to determine which cartridges would shoot with the least deviation. Teams worked out schemes for drawing the best performance from each member. And the Army Ordnance Corps delved into the mysteries of making its rifles and ammunition more accurate and user-friendly.
One of the most immediate problems facing both the Ordnance and the individual shooter was the tendency of then-current service ammunition to foul the interior of a rifle's bore. Bullet jackets at that time were drawn from an alloy of copper and nickel (cupro-nickel). This alloy had been in use since the development of ammunition for the Krag-Jorgensen rifle of 1892, but until the army switched to the Model 1906 cartridge with its 150-grain bullet at a velocity of some 2,700 fps (specifications called for an instrumental velocity of 2,640 fps at a point 78 feet from the gun), there were no significant problems. The velocity of the 1906 cartridge, however, was above the threshold at which the heat and friction of firing neatly soldered small amounts of the bullet jacket to the interior of a rifle's bore. Once this jacket fouling began to build up, it tended to build on itself and, in very short order, the barrel filled with lumpy fouling and accuracy quickly deteriorated. To compound the problem, removing the cupro-nickel jacket fouling risked permanent damage to the bore.
Townsend Whelen, one of the leading rifleman-experimenter-developers of the first half of the 20th century, was an Ordnance Corps Major in 1921, and was commanding officer at the Army's Frankford Arsenal—an ammunition plant outside Philadelphia, PA. Whelen had a lot of ammunition made with tin-plated bullets based on the French army's experience in World War I. Actually, there were three experimental lots loaded with cupro-nickel bullets, tin-plated cupro-nickel bullets and tin-plated gilding metal bullets. The lot having tin-plated cupro-nickel bullets performed best and was selected for loading and use in the National Matches for 1921. If all went well, the tin would act as a heat shield and lubricant, and also prevent cupro-nickel jacket fouling. It worked—Whelen's "tin can" ammunition shot astonishingly well.
But there was a fly in the ointment—actually, there were two flies. The first was that the tin on the bullet and the brass of the cartridge case reacted to form an electro-chemical weld between the two components. The ammunition developers knew this phenomenon. Fired normally, the cartridge case would expand to fill the chamber, break the bond between bullet and case, and allow the bullet to travel freely down the bore. As long as nothing else went wrong, there wasn't a problem. That there was another potential "wrong" was the second fly.
Shooters of the period, despite printed prohibitions, depended on grease (the most popular was a highly refined cup grease sold as "Mobilubricant") applied to the bullets to do what the tin did—insulate the bullet from the bore. Applying external lubricant to cupro-nickel bullet jackets would have been a good solution to the jacket fouling problem had it not been for the tendency of the lubricant to migrate and coat the interior of the neck portion of the chamber. There, the grease not only caused increased thrust on a rifle's locking lugs, but it also kept the case neck from expanding and upped chamber pressure to dangerous levels—to more than 70,000 psi in one test from Hatcher's Notebook. And that test was conducted using ammunition that did not have bullets and case necks welded to one another.
Despite published prohibitions in 1920 and a vivid description of the potential for disaster that accompanied each issue of 1921 National Match ammunition, many competitors at Camp Perry that year insisted on using Mobilubricant with the tin-plated bullets. Several of them paid the price of a ruined rifle for their folly (there were no significant injuries). Major General Julian Hatcher had in his collection of memorabilia a tin-plated bullet picked up on the range at Perry in 1921. The case neck was still attached to the bullet and rifling marks extended through both the bullet and the neck. "The pressure," he surmised later, "must have been enormous."
Because of the potential for harm and despite its general success, the War Department ordered the entire experimental lot of tin can ammunition withdrawn and destroyed. Few samples survived. An alternate lot of ammunition was issued for use during the remainder of the matches.
By 1922, gilding metal—an alloy of 90 percent copper and 10 percent zinc—had replaced cupro-nickel in bullet jackets and the jacket fouling problem was solved.
One of the most immediate problems facing both the Ordnance and the individual shooter was the tendency of then-current service ammunition to foul the interior of a rifle's bore. Bullet jackets at that time were drawn from an alloy of copper and nickel (cupro-nickel). This alloy had been in use since the development of ammunition for the Krag-Jorgensen rifle of 1892, but until the army switched to the Model 1906 cartridge with its 150-grain bullet at a velocity of some 2,700 fps (specifications called for an instrumental velocity of 2,640 fps at a point 78 feet from the gun), there were no significant problems. The velocity of the 1906 cartridge, however, was above the threshold at which the heat and friction of firing neatly soldered small amounts of the bullet jacket to the interior of a rifle's bore. Once this jacket fouling began to build up, it tended to build on itself and, in very short order, the barrel filled with lumpy fouling and accuracy quickly deteriorated. To compound the problem, removing the cupro-nickel jacket fouling risked permanent damage to the bore.
Townsend Whelen, one of the leading rifleman-experimenter-developers of the first half of the 20th century, was an Ordnance Corps Major in 1921, and was commanding officer at the Army's Frankford Arsenal—an ammunition plant outside Philadelphia, PA. Whelen had a lot of ammunition made with tin-plated bullets based on the French army's experience in World War I. Actually, there were three experimental lots loaded with cupro-nickel bullets, tin-plated cupro-nickel bullets and tin-plated gilding metal bullets. The lot having tin-plated cupro-nickel bullets performed best and was selected for loading and use in the National Matches for 1921. If all went well, the tin would act as a heat shield and lubricant, and also prevent cupro-nickel jacket fouling. It worked—Whelen's "tin can" ammunition shot astonishingly well.
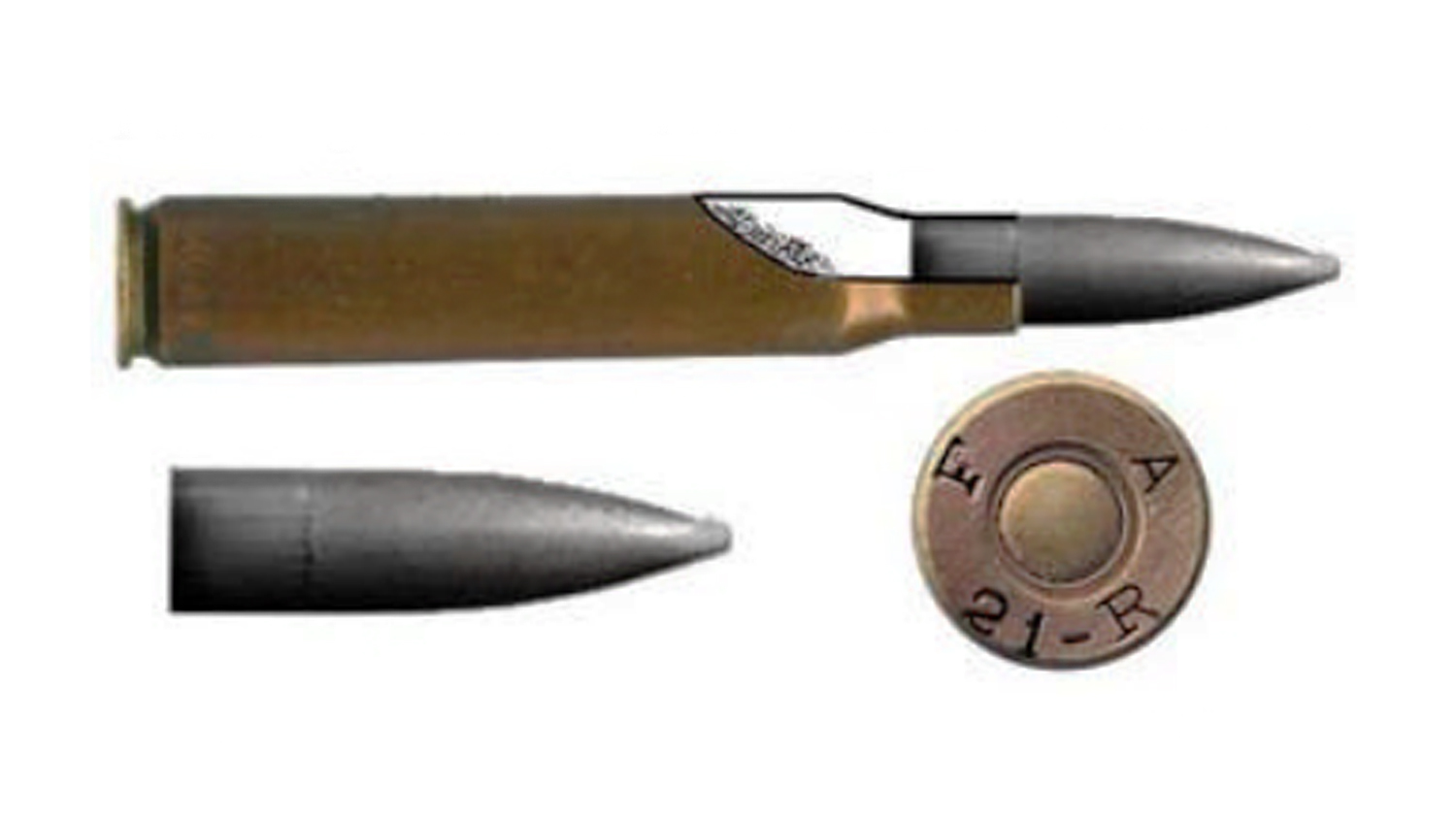
The 1921 National Match cartridge headbase was stamped with FA and 21-R.
Shooters of the period, despite printed prohibitions, depended on grease (the most popular was a highly refined cup grease sold as "Mobilubricant") applied to the bullets to do what the tin did—insulate the bullet from the bore. Applying external lubricant to cupro-nickel bullet jackets would have been a good solution to the jacket fouling problem had it not been for the tendency of the lubricant to migrate and coat the interior of the neck portion of the chamber. There, the grease not only caused increased thrust on a rifle's locking lugs, but it also kept the case neck from expanding and upped chamber pressure to dangerous levels—to more than 70,000 psi in one test from Hatcher's Notebook. And that test was conducted using ammunition that did not have bullets and case necks welded to one another.
Despite published prohibitions in 1920 and a vivid description of the potential for disaster that accompanied each issue of 1921 National Match ammunition, many competitors at Camp Perry that year insisted on using Mobilubricant with the tin-plated bullets. Several of them paid the price of a ruined rifle for their folly (there were no significant injuries). Major General Julian Hatcher had in his collection of memorabilia a tin-plated bullet picked up on the range at Perry in 1921. The case neck was still attached to the bullet and rifling marks extended through both the bullet and the neck. "The pressure," he surmised later, "must have been enormous."
Because of the potential for harm and despite its general success, the War Department ordered the entire experimental lot of tin can ammunition withdrawn and destroyed. Few samples survived. An alternate lot of ammunition was issued for use during the remainder of the matches.
By 1922, gilding metal—an alloy of 90 percent copper and 10 percent zinc—had replaced cupro-nickel in bullet jackets and the jacket fouling problem was solved.